Before I became a CNC operator, I thought machines did all the work. Press a button, and the parts come out perfectly. I couldn’t have been more wrong.
The real magic? It’s in the hands of the CNC operators who make sure everything runs smoothly.
If you’re in the machine industry, you know that well-trained operators make all the difference.
In this article I’ll share:
- What CNC operators do in a manufacturing setting.
- How their decisions impact precision, efficiency, and machine health.
- The most common challenges CNC operators face.
By the end, you’ll have a clear understanding of why CNC operators are a key factor in machine performance and business success.
Let’s begin!
1. Understanding the Role of CNC Operators
Walk into any modern manufacturing facility, and you’ll hear the hum of CNC machines at work. These machines shape metal, plastic, and wood with unmatched precision. But here’s the thing—CNC machines don’t think for themselves. That’s where CNC operators come in.
What Is CNC and Why Does It Matter?
CNC stands for Computer Numerical Control. These machines are programmed to cut, drill, and shape materials with extreme precision. Industries like furniture, advertising, decoration, and mold design depend on CNC technology to produce high-quality, repeatable parts.
But here’s what most people don’t realize—CNC machines don’t think for themselves. They follow programmed instructions, but when something goes wrong, they don’t fix themselves. That’s the CNC operator’s job.
What Do CNC Operators Actually Do?
A CNC operator doesn’t just push buttons. They handle:
- Setting Up The Machine: Loading materials, installing tools, and making sure everything is positioned correctly.
- Monitoring Production: Watching every cut, listening for unusual sounds, and catching small mistakes before they become disasters.
- Making Adjustments: Tweaking speed, depth, and tool paths to get the best quality.
- Performing Maintenance: Keeping the machine in top shape by cleaning, inspecting, and replacing worn-out parts.
In my opinion, using a user-friendly CNC machine like those from Blue Elephant can significantly improve an operator’s workflow—making their job easier and faster. CNC work is hands-on and demands patience, skill, and attention to detail, so intuitive and reliable equipment makes a real difference.
Why CNC Operators Matter To Businesses
- For Machine Dealers, Repairers, And Rental Companies: Skilled CNC operators mean fewer breakdowns, longer machine life, and happier customers. A poorly trained operator can wear out tools faster, damage parts, or even cause expensive repairs.
- For Manufacturing Businesses: CNC operators directly impact efficiency and cost. A good operator knows how to minimize waste, optimize speed, and keep production on track.
I’ve seen companies struggle because they didn’t invest in the right operators. Machines are expensive, but the right person behind them? That’s priceless.
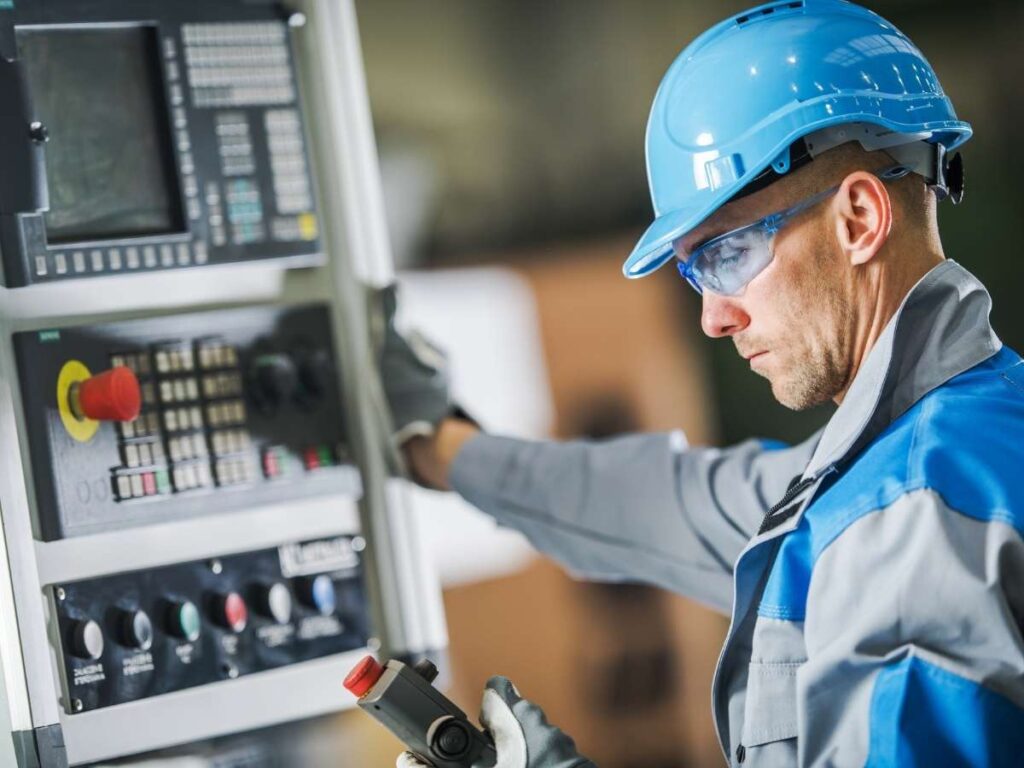
2. Core Responsibilities of a CNC Operator
CNC operators are the backbone of precision manufacturing. Their job isn’t just about running machines—it’s about controlling accuracy, efficiency, and quality at every stage of production. A single mistake in setup or monitoring can lead to wasted materials and costly downtime.
From preparing machines to maintaining safety, CNC operators have a wide range of responsibilities. Let’s break them down.
Setting Up CNC Machines
Proper setup is the foundation of every successful job. Before machining begins, the operator must:
- Load Programs: The right CNC program is uploaded and checked for errors. Even a minor coding mistake can cause production failures.
- Adjust Settings: Tool offsets, spindle speeds, and feed rates must match job specifications for optimal performance.
- Read Blueprints: Technical drawings guide the machine’s movements, so understanding dimensions and tolerances is key.
- Prepare Tools And Materials: Cutting tools are installed, raw materials are secured, and everything is verified before starting production.
I’ve learned the hard way that rushing through setup only causes problems later. Taking the time to get it right from the beginning always pays off.
Operating CNC Machinery
Once the machine is running, the operator’s job is far from over. Machines don’t always follow the script perfectly, so close monitoring is required:
- Monitor Performance: Watching for irregularities ensures early problem detection.
- Adjust Controls: Feed rates, spindle speeds, and tool paths may need fine-tuning for accuracy.
- Manage Cutting Parameters: Adjusting depth and speed ensures smooth operation and extends tool life.
Machining is never a hands-off process. Operators keep a close eye on production to prevent costly mistakes.
Quality Control and Inspection
Producing parts isn’t enough—they have to meet strict quality standards. Precision is everything, which means frequent checks, including:
- Measuring Finished Parts: Using calipers, micrometers, and gauges to confirm accuracy.
- Comparing Against Blueprints: Ensuring each part matches design specifications.
- Routine Inspections: Spot-checking throughout production prevents defects from piling up.
Nothing is worse than finishing a job, only to realize every part is out of spec. Skipping inspections is a mistake you only make once.
Machine Maintenance and Troubleshooting
CNC machines need regular care to function properly. Ignoring maintenance can lead to breakdowns and expensive repairs. Operators are responsible for:
- Routine Maintenance: Cleaning chips, lubricating parts, and replacing worn-out tools.
- Identifying Issues: Noticing unusual sounds, vibrations, or cutting errors that signal a problem.
- Reporting Problems: If troubleshooting doesn’t fix the issue, operators notify maintenance teams before small problems escalate.
I once ignored a strange noise coming from the machine. A few hours later, a tool broke mid-cut, damaging the part and the spindle. That was the last time I ignored an early warning sign.
Safety Compliance
CNC shops can be hazardous environments, so safety is a top priority. Operators must:
- Follow Safety Regulations: Strict protocols are in place for handling machines and materials.
- Wear Protective Gear: Safety glasses, gloves, and hearing protection help prevent injuries.
- Maintain A Clean Workspace: Loose tools, coolant spills, or unsecured materials can create serious hazards.
One loose bolt or unsecured part can turn into a dangerous projectile. A clean and organized workspace is a safe workspace.
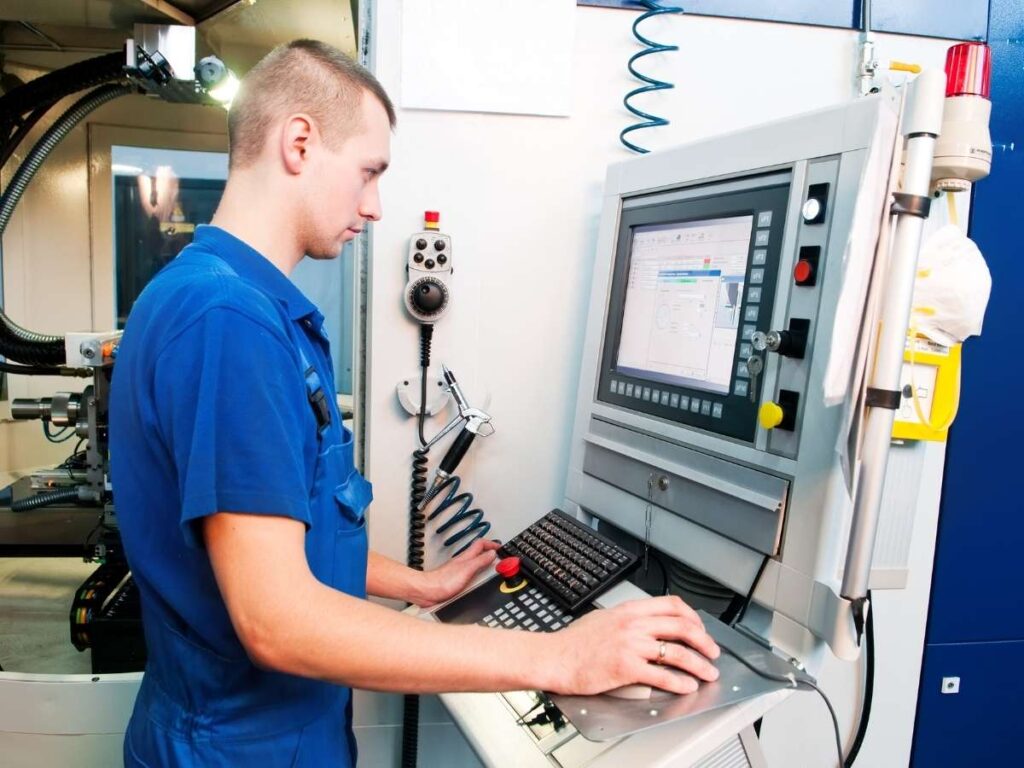
3. Skills and Qualifications Needed for CNC Operators
Running a CNC machine isn’t just about pushing buttons—it’s about making precise adjustments, solving problems, and keeping production moving. Skilled operators make all the difference in efficiency and quality. But what exactly does it take to be a great CNC operator?
Let’s break down the technical knowledge, soft skills, and training that set the best operators apart.
Technical Skills
A CNC operator needs a solid understanding of machines, programming, and precision tools to do the job well. Without these technical skills, production errors can pile up quickly.
- Understanding CNC Software And Controls: Operators must know how to use G-code and M-code—the programming languages that control CNC machines. G-code tells the machine where and how to move, while M-code handles non-movement functions like turning coolant on and off.
- Machine Setup And Calibration: Each job requires setting up tools, adjusting offsets, and calibrating the machine to meet exact specifications. A small miscalculation can lead to scrap parts and wasted materials.
- Reading Blueprints And Technical Drawings: Precision starts with understanding the details. Operators must read engineering drawings, tolerances, and part dimensions to make sure the final product meets exact standards.
I’ve seen operators skip double-checking a blueprint, only to realize too late that they used the wrong tool for the job. A few extra minutes of planning can save hours of rework.
Soft Skills
Technical skills are essential, but the best CNC operators also have strong soft skills to handle the fast-paced world of manufacturing.
- Attention To Detail: A CNC machine won’t correct a mistake in the program. Operators must be precise in their measurements, settings, and inspections.
- Problem-Solving: Unexpected issues—like tool wear, material inconsistencies, or program errors—happen all the time. The ability to think quickly and troubleshoot problems is what separates a good operator from a great one.
- Time Management: In manufacturing, every second counts. An operator must set up machines efficiently, monitor multiple jobs, and keep downtime to a minimum.
- Communication And Teamwork: Operators work closely with programmers, engineers, and quality control teams. Clear communication prevents mistakes and keeps production running smoothly.
Certifications and Training
You don’t need a four-year degree to become a CNC operator, but proper training and certification can open more opportunities.
- Industry Certifications: Organizations like the National Institute for Metalworking Skills (NIMS) offer certifications that validate an operator’s skills. Some companies also require OSHA safety training to meet workplace safety standards.
- Apprenticeship Programs: Many operators learn on the job through apprenticeship programs. These programs combine hands-on training with classroom instruction.
- Continuous Learning: CNC technology is always evolving. Operators who stay updated on new tools, software, and machining techniques will always be in demand.
I’ve seen operators with years of experience struggle when a new machine arrived in the shop. Those who kept learning adapted quickly, while others fell behind.
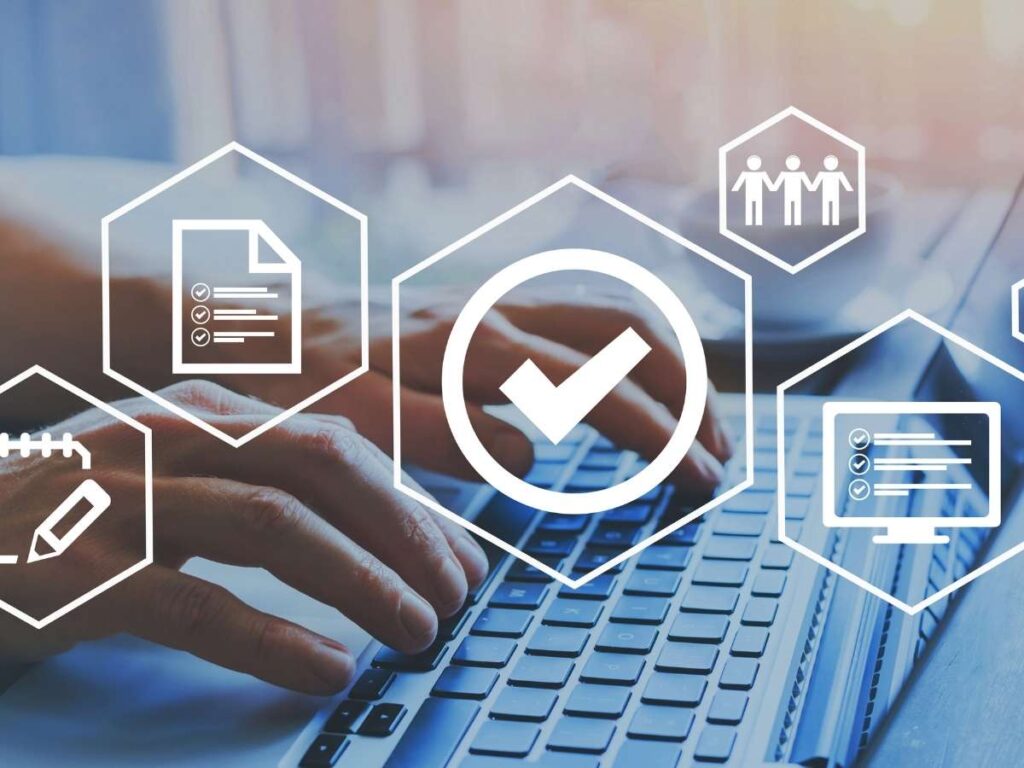
4. Why CNC Operators Are Crucial for Businesses
CNC machines can run thousands of parts with incredible accuracy—but only if the right person is behind the controls. A machine is only as good as its operator. Without skilled CNC operators, production slows, quality drops, and businesses lose money.
How CNC Operators Help B2B Businesses
If you sell, rent, or service CNC machines, you’ve probably seen what happens when someone without experience runs one. It’s not pretty.
- Keeping Machines Running Longer: A skilled operator knows how to set up tools, adjust feeds, and avoid overloading the machine. This extends the life of expensive equipment.
- Preventing Costly Repairs: When an untrained operator misuses a machine, it’s not just a mistake—it’s an expensive repair waiting to happen. Tool crashes, overheating, and improper maintenance add up fast.
- Protecting Rental Machines: CNC rental businesses rely on operators who know how to handle machines properly. A careless mistake on a rental unit can mean a damaged spindle, lost revenue, or even a total replacement.
Why CNC Operators Matter for B2C Businesses
For businesses producing custom parts, furniture, signage, or molds, CNC operators ensure precision and consistency. Without them, manufacturing would be slower, less reliable, and full of errors.
- Precision Cutting for High-Quality Furniture and Decoration: CNC machines can cut with extreme accuracy, but only if the operator understands tolerances, tool wear, and material properties.
- Faster Production for Advertising Materials: Sign-making and advertising require quick turnarounds. A good CNC operator optimizes feed rates and tool paths to get jobs done faster without sacrificing quality.
- Efficiency in Mold Design and Manufacturing: Mold-making is all about getting every detail perfect. Even the smallest mistake can ruin an entire production run. Skilled CNC operators help businesses avoid costly rework.
5. How to Hire or Train a CNC Operator for Your Business
Finding a skilled CNC operator isn’t just about filling a position—it’s about keeping your machines running smoothly, minimizing errors, and maintaining efficiency. The right operator can save you money, while the wrong one can cost you in wasted materials, downtime, and repairs.
So how do you find the right person? And if you already have employees, how do you train them to become CNC experts? Let’s break it down.
Key Factors to Consider When Hiring a CNC Operator
When hiring, consider:
- Experience Level and Skill Assessment:
- Has the candidate worked with similar CNC machines before?
- Can they read blueprints, program G-code, and troubleshoot issues?
- Have they worked in high-production or custom machining environments?
- Industry-Specific Expertise:
- Woodworking, metal fabrication, mold-making, and signage all have different CNC processes.
- Some industries require more precision, while others focus on speed and efficiency.
- A CNC operator experienced in one industry may need extra training for another.
- Understanding Company-Specific CNC Needs:
- Are you running high-volume production or custom one-off jobs?
- Does your business focus on tight tolerances or general fabrication?
- Will the operator need to program machines or just run pre-set programs?
Training and Upskilling In-House Employees
Sometimes, the best CNC operators are already working for you. If you have machine shop employees who are eager to learn, investing in their training can be a smart long-term move.
Ways to upskill your team:
- CNC Certification Programs:
- Enroll employees in industry-recognized programs like NIMS (National Institute for Metalworking Skills).
- Some technical schools offer short-term CNC operator training that covers G-code programming, tool selection, and machine calibration.
- OSHA safety training can also help reduce workplace accidents.
- Hands-On Workshops and Mentorship:
- Pair new operators with experienced machinists for on-the-job training.
- Set up real-world projects where employees can practice setups, tool changes, and part inspections.
- Encourage employees to shadow senior operators to learn industry best practices.
- Encouraging Continuous Learning:
- CNC technology is constantly evolving. Operators who don’t keep learning get left behind.
- Provide access to online courses, industry conferences, and CNC software updates.
- Host monthly skill-building sessions to discuss common mistakes, troubleshooting methods, and efficiency tips.
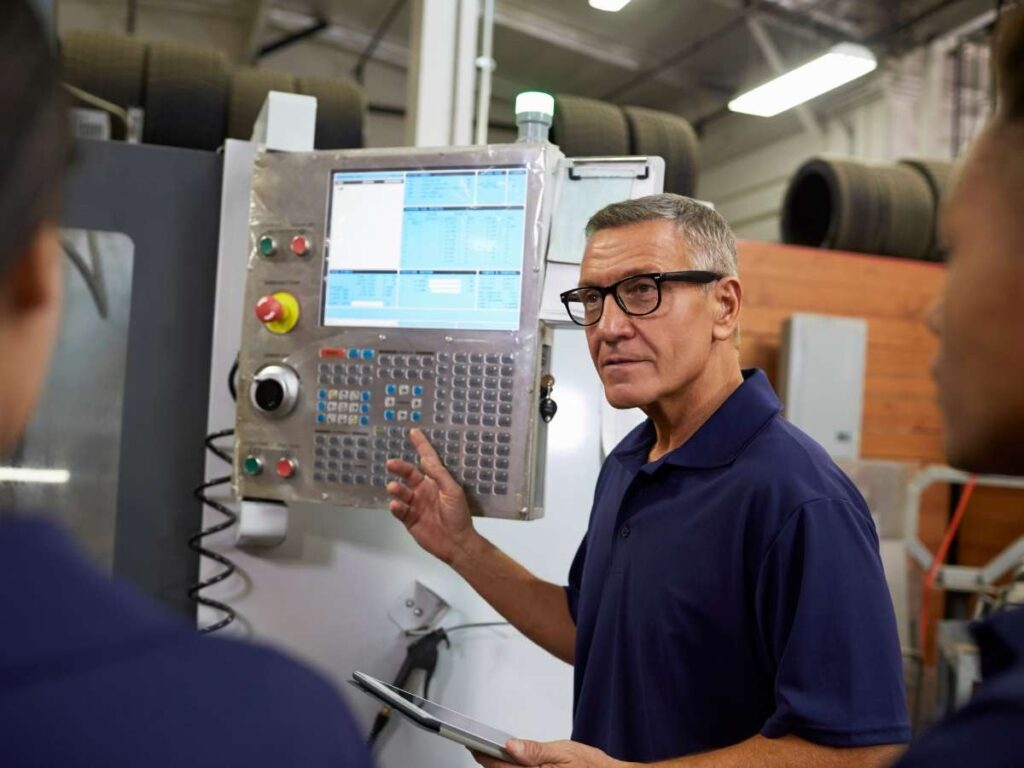
6. CNC Operators vs. CNC Programmers: What’s the Difference?
I remember the first time I worked with a CNC programmer. I had been running machines for a while—setting up tools, adjusting feeds, and keeping everything running smoothly. Then, a programmer handed me a fresh G-code file. It looked like a foreign language to me at the time. That’s when I realized—operators and programmers may work together, but their roles are completely different.
If you’re hiring for a CNC team or just trying to understand the differences, here’s a quick comparison:
Aspect | CNC Operator | CNC Programmer |
Main Role | Runs and maintains CNC machines. | Writes the code that controls CNC machines. |
Key Responsibilities | – Sets up tools and materials. – Monitors machine operation. – Adjusts settings during production. – Inspects finished parts for accuracy. – Troubleshoots machine issues. | – Creates G-code and M-code. – Designs and optimizes tool paths. – Programs machines based on blueprints. – Reduces production time and material waste. – Works with operators to refine programs. |
Work Environment | On the shop floor, working directly with machines. | In an office or programming station, designing CNC programs. |
Required Skills | – Reading blueprints and technical drawings. – Operating and maintaining CNC machines. – Measuring and inspecting finished parts. – Making manual adjustments when needed. | – Writing and modifying G-code and M-code. – Using CAD/CAM software (Mastercam, Fusion 360). – Understanding machining speeds, feeds, and cutting paths. – Optimizing tool paths for efficiency. |
Interaction with Machines | Direct—loads materials, starts jobs, and adjusts settings during operation. | Indirect—writes programs but does not typically run machines. |
Collaboration | Works with programmers to ensure machine code runs correctly. | Works with operators to adjust programs for real-world accuracy. |
When to Hire? | If you need someone to run and maintain machines, check quality, and make real-time adjustments. | If you need someone to write and optimize CNC programs, improving efficiency and reducing cycle times. |
CNC operators bring designs to life, while CNC programmers write the instructions that make it happen. Both roles are crucial to efficient, high-quality manufacturing. If you’re looking to build a CNC team, understanding when to hire an operator, a programmer, or both can help improve productivity and profitability.
7. Future Trends for CNC Operators
CNC technology is evolving fast. Automation, AI, and machine learning are changing the way machines operate. But does that mean CNC operators will become obsolete? Not at all.
Instead of replacing operators, these advancements are reshaping their role. The best CNC operators will be the ones who adapt, learn new technologies, and stay ahead of industry trends.
Automation’s Impact on CNC Operator Roles
Manufacturers are investing heavily in automation. CNC machines can now:
- Run Longer With Minimal Human Intervention: Robotic arms and automated tool changers reduce manual setup time.
- Perform Real-Time Error Detection: Sensors track cutting performance and detect tool wear.
- Optimize Cutting Paths On Their Own: Some machines adjust feed rates and speeds for better efficiency.
So, what does this mean for CNC operators? Instead of just running machines, operators will take on more technical roles: overseeing automation, troubleshooting complex issues, and optimizing production.
I once saw a CNC lathe running fully automated. It looked like it didn’t need an operator—until the tool wore out unexpectedly. A skilled operator had to step in, recalibrate, and get production back on track. Automation helps, but human expertise is still essential.
The Rise of AI and Machine Learning in CNC Machining
AI is transforming CNC machining by:
- Predicting Machine Failures: AI systems analyze data and detect early signs of wear before breakdowns happen.
- Improving Part Accuracy: Machine learning algorithms optimize tool paths based on real-time conditions.
- Reducing Human Error: AI-powered systems can fine-tune machining parameters without operator input.
But here’s the catch—AI still needs experienced operators to interpret data and make judgment calls. Machines can optimize, but they can’t think critically like a human.
How CNC Operators Can Adapt to Technological Advancements
To stay relevant in the CNC industry, operators should:
- Learn CNC Programming: Understanding G-code, CAD/CAM software, and AI-driven optimizations will be a game-changer.
- Develop Troubleshooting Skills: The more automated a system becomes, the more critical it is to know how to fix unexpected issues.
- Stay Updated on New Technologies: Attending industry events, online courses, and hands-on training sessions will keep operators competitive.
CNC technology is advancing, but operators who embrace change will always have a place in the industry. Automation and AI may handle repetitive tasks, but skilled operators will still be needed for problem-solving, quality control, and process optimization.
The future of CNC isn’t about replacing operators—it’s about making them more valuable than ever.
Conclusion
When I first ran a CNC machine, I thought it worked on autopilot. But now I know—it’s the operator who makes the difference.
If you’re building a precision-driven operation, you don’t just need a machine—you need the right machine and the right people.
At Blue Elephant, we design CNC machines that support smart, efficient, operator-friendly workflows.
Contact us today to explore solutions that keep your operators performing at their best!
Recommended Reads for You
If you’re looking for more insights, we’ve put together a list of helpful articles that you might enjoy:
Still haven’t found what you’re looking for? Don’t hesitate to contact us. We’re available around the clock to assist you.