There’s nothing worse than buying a CNC machine and realizing later that it’s not what you needed. I’ve been there. A supplier once recommended a machine to me, swearing it was perfect. It wasn’t.
The specs were wrong, the software was clunky, and I ended up wasting time and money on something that didn’t fit my shop’s needs.
That mistake taught me a valuable lesson: knowing CNC machine names matters. The right name helps you compare features, find reliable brands, and avoid costly mistakes. But the problem? Most resources don’t make it easy. Some lists mix up machine types, others only focus on one industry.
That’s why I wrote this guide. You’ll get a straightforward list of CNC machine names, grouped by type, brand, and application. No fluff, no guesswork, just a clear reference to help you make the right choice. By the end, you’ll have the knowledge to pick the right CNC machine with confidence.
Let’s start!
Quick Comparison
Before we dive deeper into each CNC machine, here’s a quick side-by-side comparison. This table gives you a glimpse of what each machine does best, so you can start narrowing down which one fits your needs. Whether you’re cutting metal, engraving wood, or machining high-precision parts, this chart will help you see the differences at a glance:
CNC Machine Type | Best For | Cutting Method | Common Materials | Precision Level | Speed | Key Benefit |
CNC Router | Woodworking, sign-making, prototyping | Rotating cutting tool | Wood, plastic, soft metals | High | Fast | Best for intricate wood and plastic designs |
CNC Milling Machine | Metal fabrication, prototyping, custom parts | Rotating cutting tool | Aluminum, steel, brass, plastics | Very High | Moderate | Excellent for detailed metalwork |
CNC Lathe | Shafts, cylindrical parts, threading | Rotating workpiece, stationary cutting tool | Metal, plastic | High | Fast | Perfect for making precise round parts |
CNC Laser Cutter | Metal engraving, industrial cutting, detailed cuts | High-powered laser beam | Metal, acrylic, wood, glass | Extremely High | Very Fast | Delivers clean, precise cuts with minimal finishing needed |
CNC Plasma Cutter | Heavy metal cutting, fabrication shops | Superheated plasma arc | Steel, aluminum, stainless steel | Moderate | Very Fast | Ideal for fast, cost-effective metal cutting |
CNC Waterjet Cutter | Stone, glass, heat-sensitive materials | High-pressure water and abrasives | Metal, stone, glass, composites | High | Slow-Moderate | No heat damage, cuts through almost any material |
CNC EDM Machine | Hardened metals, micro-machining, precision molds | Electrical discharge (sparks) | Titanium, hardened steel, tungsten | Extremely High | Slow | Best for cutting extremely tough materials with unmatched accuracy |
Now that you’ve seen the big picture, let’s break it down further.
Each CNC machine has its own strengths, limitations, and ideal uses and the next sections will help you find the perfect match for your work.
1. CNC Routers
The first time I used a CNC router, I was amazed.
I had spent hours trying to carve a simple sign by hand, only to mess up the lettering at the last minute. Then, I loaded the same design into a CNC router, pressed a button, and watched as the machine carved perfect letters in minutes. No shaky lines. No wasted material. Just a clean, professional cut.
A CNC router can carve, engrave, and shape materials like wood, plastic, and even metal.
Some people call it a CNC carving machine or CNC engraving machine because of how precise it is. Unlike handheld routers, this machine follows a digital design, so every cut is exactly the same whether you make one piece or a hundred.
CNC routers are widely used in:
- Furniture making – Creating cabinet doors, custom furniture, and decorative woodwork.
- Sign-making – Carving letters and intricate designs into wood, acrylic, and metal.
- Mold production – Crafting precise molds for casting and manufacturing.
- Hobby projects – Perfect for DIYers making detailed carvings and engravings.
If you’ve ever seen a beautifully carved wooden sign or an ornate piece of furniture, chances are a CNC router was involved.
Key Features
- Computer-controlled cutting – Just upload a design, and the machine follows it precisely.
- Multi-axis movement – Most routers move in3 (X, Y, and Z), but advanced models go up to 5 axes for more complex cuts.
- Spindle speed control – Adjust the speed for different materials to get clean, smooth edges.
- Vacuum bed or clamps – Holds the material in place to prevent shifting.
Specifications
While specs vary by model, most CNC routers have:
- Cutting area: From small desktop sizes (12″x12″) to large industrial sizes (5’x10′ or bigger).
- Spindle power: Ranges from 800W to 12kW, depending on the material.
- Software compatibility: Works with CAD/CAM software like Fusion 360, VCarve, and AutoCAD.
- Material support: Cuts wood, MDF, acrylic, PVC, and even soft metals like aluminum.
A CNC router doesn’t just improve accuracy, it saves you time, reduces waste, and allows you to produce high-quality work with less effort. Whether you’re making furniture, signs, or detailed carvings, having the right machine makes all the difference.
At Blue Elephant, we specialize in CNC routers that combine power and precision, helping businesses and craftsmen bring their ideas to life.
2. CNC Milling Machines
I couldn’t believe how precise CNC Milling machines it was. I had spent hours trying to shape a metal piece using a manual mill, adjusting knobs, rechecking measurements, and still making mistakes.
But with a CNC milling machine?
The cuts were exact, smooth, and repeatable without me having to guide the tool by hand.
A CNC milling machine, sometimes called a CNC mill, is a computer-controlled machine that removes material from a solid block to create a finished part. Unlike CNC routers, which are great for softer materials like wood and plastic, CNC mills are designed for metal, hard plastics, and even composites.
CNC mills are commonly used in:
- Metalworking: Cutting, drilling, and shaping aluminum, steel, and brass.
- Aerospace & Automotive: Creating engine parts, brackets, and frames.
- Prototyping: Manufacturing small batches of test parts before mass production.
- Custom manufacturing: Making detailed parts for machines, medical devices, and tools.
I once met a machinist who used a CNC mill to make custom motorcycle parts. Every part fit perfectly because the machine cut them to exact specifications.
Key Features
- Multi-axis control: Moves in 3,4, or even 5 directions to shape complex parts.
- Automatic tool changes: Some models switch tools automatically for different cutting tasks.
- High spindle speed: Lets you cut through tough materials with precision.
- Coolant systems: Keeps the machine and material from overheating.
Specifications
CNC mills vary in size, but most have:
- Worktable size: Small mills fit on a bench, while industrial ones take up entire rooms.
- Spindle power: Ranges from 1HP to over 30HP, depending on material thickness.
- Software compatibility: Works with CAD/CAM programs like Mastercam, SolidWorks, and Fusion 360.
- Material support: Cuts steel, aluminum, brass, titanium, and more.
If you work with metal parts or need precise, repeatable cuts, a CNC milling machine can save time and reduce waste. I learned the hard way that manual machining leaves too much room for error. But with a CNC mill, you can set up a design once and get perfect results every time.
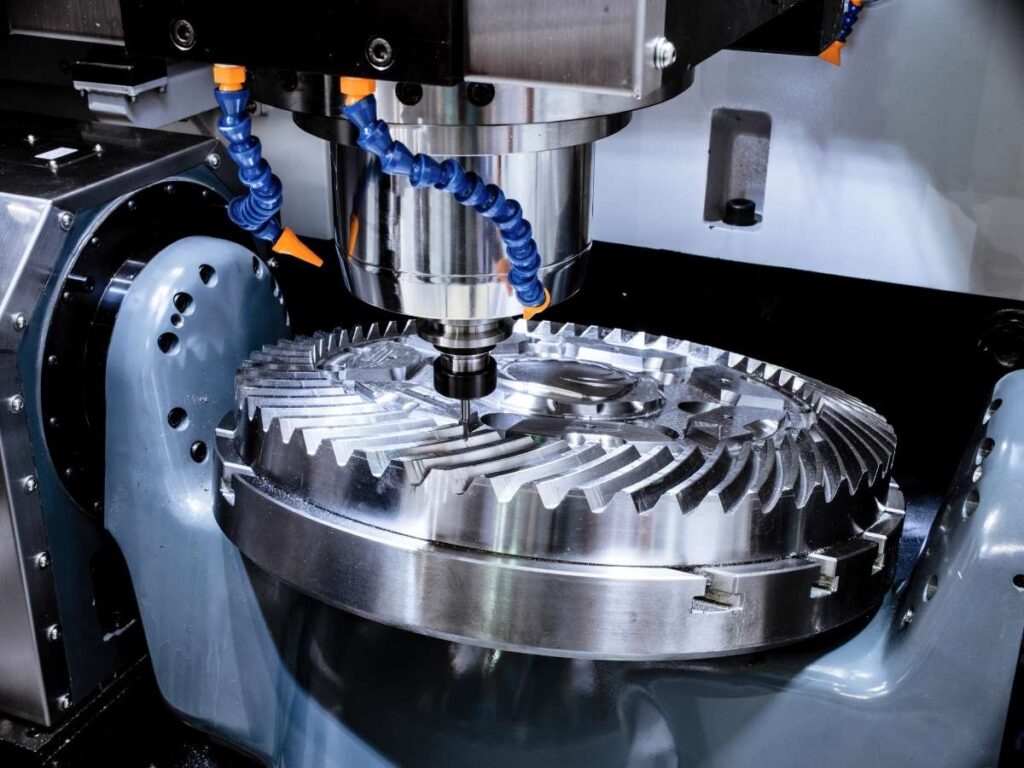
3. CNC Lathes
A CNC lathe, sometimes called a CNC turning center, is designed to rotate a workpiece while a cutting tool removes material. It’s the go-to machine for making cylindrical parts with precision. Unlike manual lathes, which require constant adjustments, a CNC lathe follows a digital program, making each part exactly the same, every time.
If you need round or symmetrical parts, a CNC lathe is the best tool for the job. These machines are commonly used in:
- Automotive and Aerospace: Producing shafts, bushings, and engine components.
- Metalworking: Cutting screws, bolts, and fasteners.
- Medical Industry: Manufacturing implants and surgical tools.
- Custom Manufacturing: Creating custom parts with high accuracy.
In fact, I once met a machinist who used a CNC lathe to make precision rifle barrels. Every barrel had to be identical, with no room for error. His CNC lathe delivered the perfect cut, every time.
Key Features
- Rotating workpiece: The material spins while the cutting tool removes material.
- Multi-tool capability: Some models switch between different tools automatically.
- High-speed spindle: Allows for faster cutting and smoother finishes.
- Live tooling: Some CNC lathes can drill, mill, or cut threads in a single setup.
Specifications
CNC lathes come in different sizes, but most have:
- Chuck size: The part-holding mechanism ranges from 6 inches to over 24 inches in diameter.
- Spindle speed: Can reach 4,000 RPM or higher, depending on the material.
- Tool capacity: Some machines hold 10+ tools, allowing for multiple operations.
- Software compatibility: Works with CAD/CAM software like Mastercam and SolidWorks.
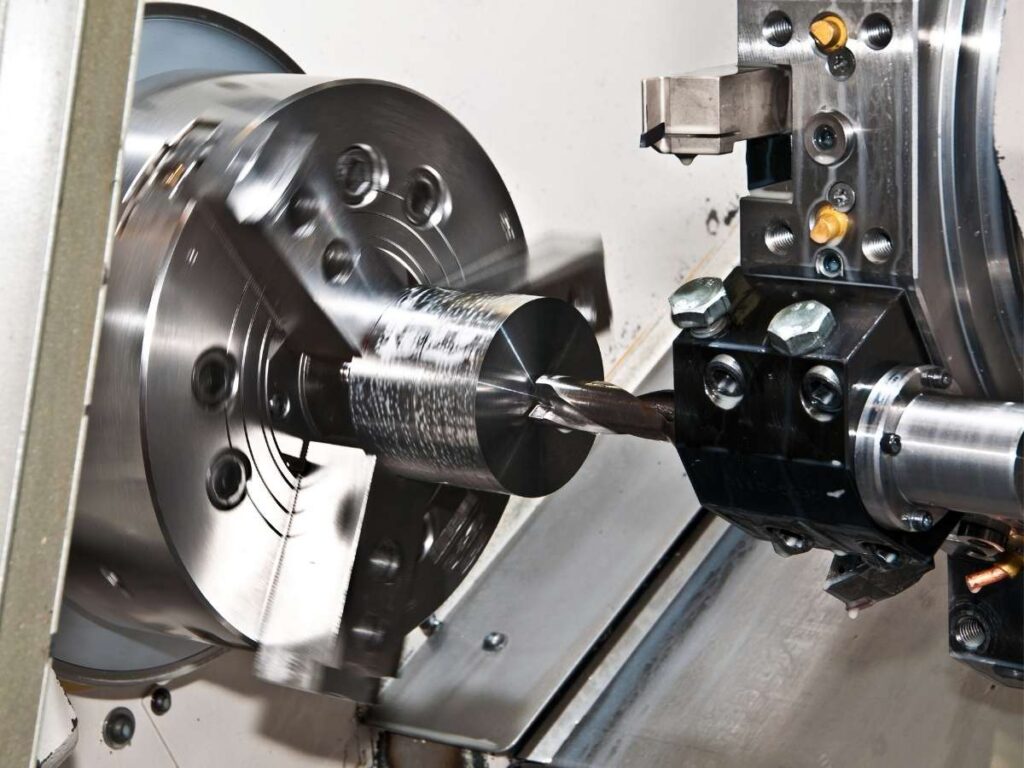
4. CNC Laser Cutting Machines
I still remember the first time I saw a CNC laser cutting machine in action. A thin, bright beam sliced through metal like it was paper, clean edges, no rough spots, no wasted material. Compared to traditional cutting tools, it was like magic.
But it wasn’t magic, it was precision engineering.
A CNC laser cutting machine, sometimes called a laser cutter, uses a high-powered laser beam to cut through materials. The machine follows a programmed design, moving the laser along precise paths to create detailed cuts, engravings, or perforations. Unlike manual cutting tools, laser cutters don’t rely on physical contact, which means less wear and tear on tools and smoother results.
Laser cutting is used across many industries, especially where clean, detailed cuts are needed. Common applications include:
- Metal Fabrication: Cutting stainless steel, aluminum, and brass for machine parts.
- Sign-Making and Engraving: Etching logos, lettering, and intricate designs onto wood, acrylic, or glass.
- Electronics Industry: Creating circuit boards and small, precision parts.
- Automotive and Aerospace: Cutting lightweight metal parts with high accuracy.
Key Features
- Non-contact cutting: The laser never touches the material, reducing tool wear.
- High precision: Can cut designs with extreme detail, down to fractions of a millimeter.
- Works with multiple materials: Cuts metals, plastics, wood, glass, and even some fabrics.
- Minimal heat distortion: The laser’s focused heat prevents warping in thin materials.
Specifications
- Laser power: Ranges from 30W for engraving to 12kW or more for heavy-duty metal cutting.
- Cutting speed: Depends on material and power, but high-speed models cut thin metal in seconds.
- Work area size: From compact desktop versions (12″x12″) to industrial setups (5’x10′ or more).
- Software compatibility: Works with AutoCAD, CorelDRAW, and LightBurn for design processing.
If precision, speed, and clean cuts matter to your business, a CNC laser cutting machine is a smart investment. Whether you’re cutting metal parts, engraving signage, or working with complex designs, a quality laser cutter can save time and reduce material waste.
At Blue Elephant, we design high-performance CNC laser cutting machines built for accuracy, efficiency, and durability. Explore our models and find the right machine for your needs.
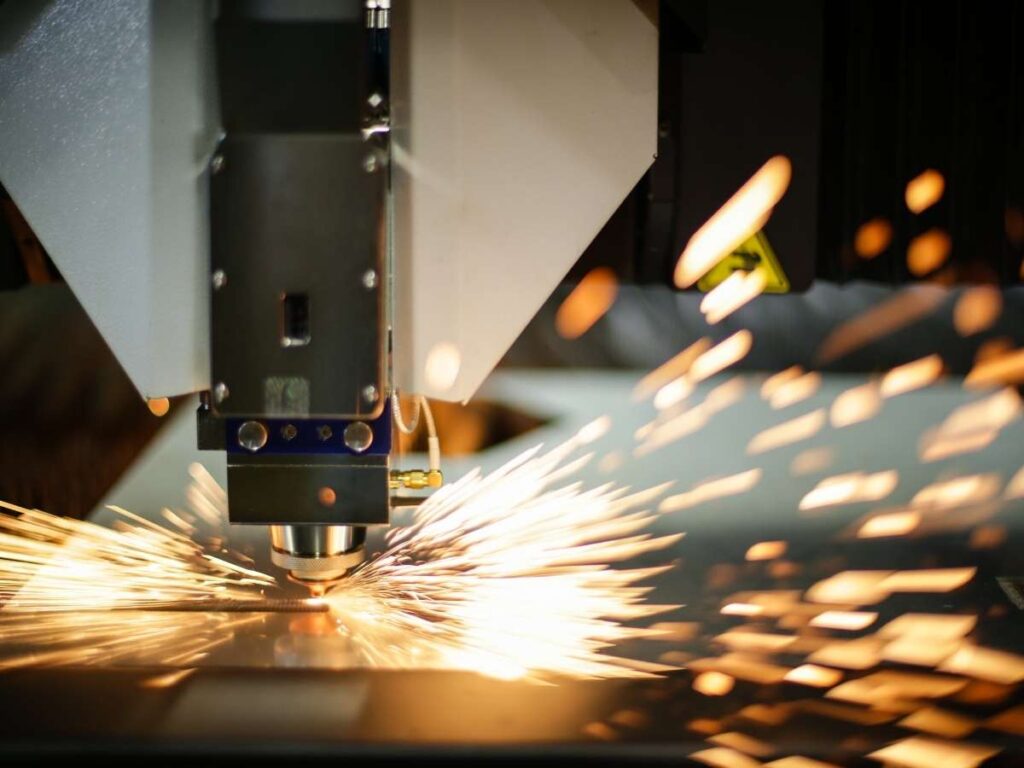
5. CNC Plasma Cutting Machines
The first time I used a CNC plasma cutter, I was blown away. I had spent years using saws and grinders to cut metal, but this machine made it effortless. A bright plasma arc tore through thick steel in seconds, fast, efficient, and with way less effort.
A CNC plasma cutting machine, often called a plasma cutter, uses a superheated plasma arc to slice through metal. Unlike laser cutters, which use light, plasma cutters use electrically charged gas to create intense heat. This makes them ideal for cutting thick, conductive metals like steel and aluminum.
Plasma cutters are built for heavy-duty metal cutting. They are widely used in:
- Metal Fabrication Shops: Cutting steel sheets and plates for construction and machinery.
- Automotive and Aerospace: Shaping chassis parts and metal components.
- Shipbuilding and Heavy Industry: Cutting thick steel for structural parts.
- DIY and Custom Metalwork: Creating metal art, gates, and industrial signs.
A welder once told me that before getting a CNC plasma cutter, he spent hours cutting and grinding metal. Now, he just loads a design, hits start, and gets clean cuts in minutes.
Key Features
- Cuts thick metal fast: Easily slices through steel, stainless steel, and aluminum.
- Works on rough, painted, or rusted surfaces: The plasma arc burns through imperfections.
- Cost-effective for large-scale cutting: Cheaper than laser cutting for thick materials.
- Can handle large workpieces: Ideal for industrial metal sheets and heavy parts.
Specifications
- Plasma power: Ranges from 30A for thin sheets to 400A for thick industrial cutting.
- Cutting thickness: Can cut metal from 1/8-inch up to 2 inches or more.
- Cutting speed: Faster than sawing or grinding, but slower than laser cutting on thin materials.
- Work area size: Typically ranges from 4’x4’ to 6’x12’ or larger for heavy-duty work.
- Software compatibility: Works with AutoCAD, Fusion 360, and SheetCAM for design setup.
If you work with thick metal and need fast, efficient cuts, a CNC plasma cutter is a solid choice. It’s perfect for fabrication shops, metalworkers, and businesses that need power and durability over fine detail.
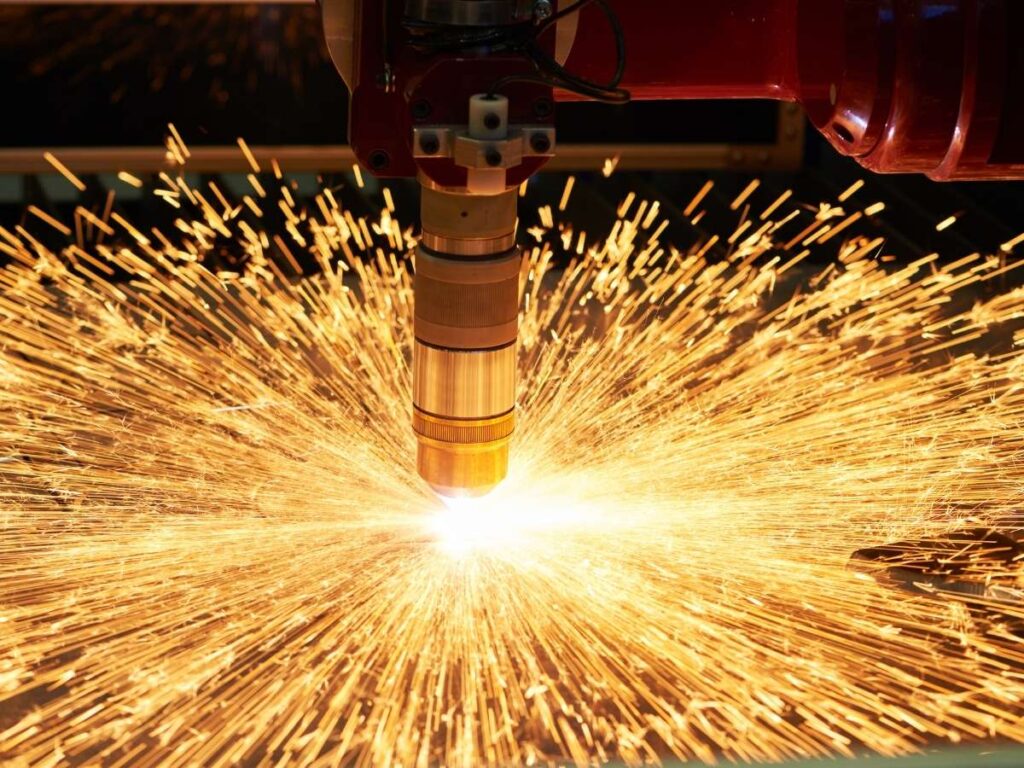
6. CNC Waterjet Cutting Machines
Not all cutting methods involve heat. The first time I saw a CNC waterjet cutting machine, I was amazed. Instead of a hot blade or plasma arc, it used a high-pressure stream of water mixed with abrasive particles to cut through metal, stone, and even glass.
It was fast, precise, and didn’t leave burn marks or heat distortion on the material.
A CNC waterjet cutter is a cold-cutting machine that uses water pressurized up to 60,000 PSI or more to slice through materials. Because it doesn’t use heat, it’s perfect for materials that would otherwise melt, warp, or crack under intense temperatures.
Waterjet cutting is widely used in industries that require clean cuts without thermal damage. Common applications include:
- Aerospace: Cutting titanium and carbon fiber without affecting material properties.
- Metal Fabrication: Creating precise steel and aluminum parts for construction.
- Stone and Tile Industry: Cutting marble, granite, and ceramics for flooring and countertops.
- Glass Cutting: Shaping thick glass panels without cracking.
- Food Processing: Some waterjet cutters even slice food like frozen meat and vegetables.
I once spoke to a shop owner who used to cut stone manually. The dust, cracks, and wasted material were constant headaches. After switching to a waterjet cutter, his cuts were perfect every time, with no cracks and less waste.
Key Features
- Cold cutting: No heat-affected zones, preventing warping or melting.
- Cuts almost any material: Works on metal, stone, glass, composites, and even rubber.
- High precision: Can cut intricate shapes with tight tolerances.
- Eco-friendly: Uses only water and abrasives, reducing hazardous fumes.
Specifications
- Pressure range: Typically 60,000 to 90,000 PSI for industrial models.
- Cutting thickness: Can cut materials up to 8 inches thick, depending on pressure and nozzle size.
- Work area size: Ranges from 4’x4′ for small shops to 10’x20′ for industrial setups.
- Software compatibility: Works with AutoCAD, Fusion 360, and IGEMS.
If you need precise cuts without heat distortion, a waterjet cutter is worth considering. Whether you’re working with metal, glass, or stone, this machine offers clean, precise, and versatile cutting.
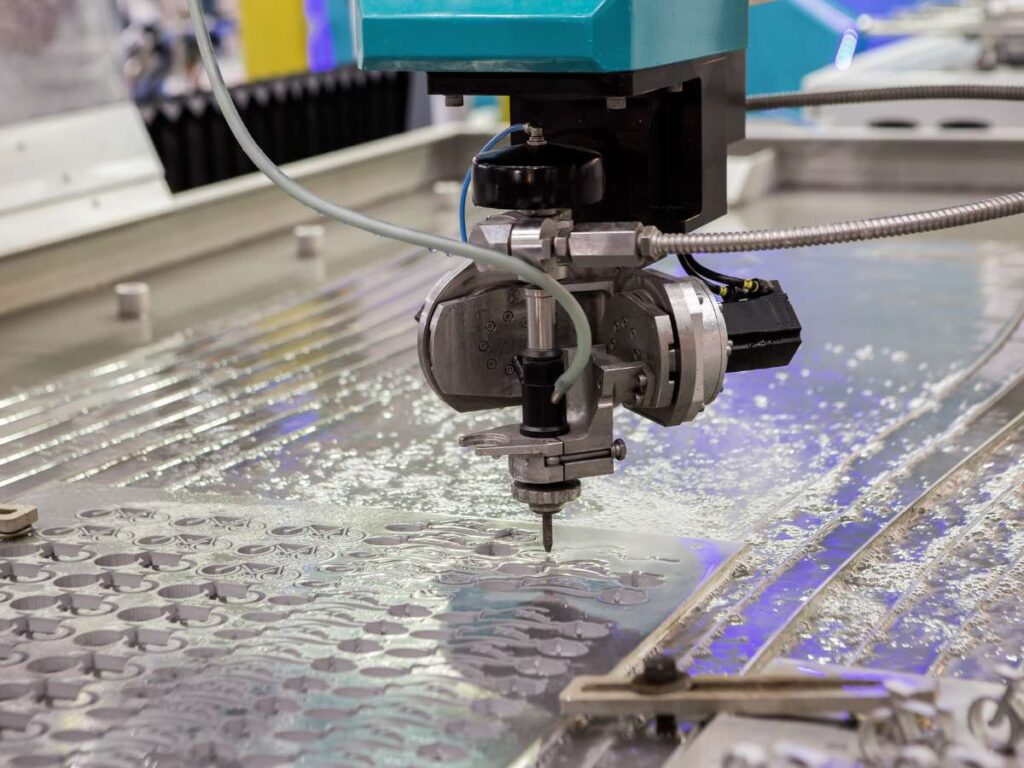
7. CNC EDM Machines
Some materials are just too tough for traditional cutting methods. I’ve seen tools wear down, blades break, and machines struggle to make precise cuts in hardened metal.
That’s when I learned about CNC EDM machines. Instead of relying on force, they use electric sparks to gradually erode the material, shaping it with incredible detail.
It’s not the fastest method, but when precision is everything, nothing else comes close.
A CNC EDM (Electrical Discharge Machining) machine, sometimes called a CNC spark eroder or wire EDM, removes material using high-frequency electrical discharges. The machine sends controlled sparks between a metal workpiece and an electrode or wire, wearing away the material bit by bit without ever making direct contact.
EDM machines are perfect for hard metals and detailed parts. They are commonly used in:
- Aerospace and Automotive: Cutting hardened steel and titanium for precision parts.
- Tool and Die Making: Creating molds, dies, and intricate metal components.
- Medical Industry: Producing surgical tools and micro-components.
- Electronics Manufacturing: Cutting fine parts for circuit boards and connectors.
Key Features
- Cuts without physical contact: Reduces tool wear and material stress.
- Works on hardened materials: Cuts tungsten, titanium, and carbide with ease.
- Can create highly detailed parts: Ideal for micro-cutting and fine details.
- Uses dielectric fluid: Helps control sparks and cools the workpiece.
Specifications
- Cutting speed: Slower than laser or plasma, but highly precise.
- Wire diameter (for wire EDM): Typically 0.004″ to 0.012″, depending on detail level.
- Workpiece size: Varies from small precision parts to large industrial molds.
- Software compatibility: Works with Mastercam, PowerMill, and ESPRIT.
If you work with hardened metals, micro-components, or intricate designs, an EDM machine is hard to beat. It’s not the fastest cutting method, but for complex, high-precision parts, nothing else comes close.
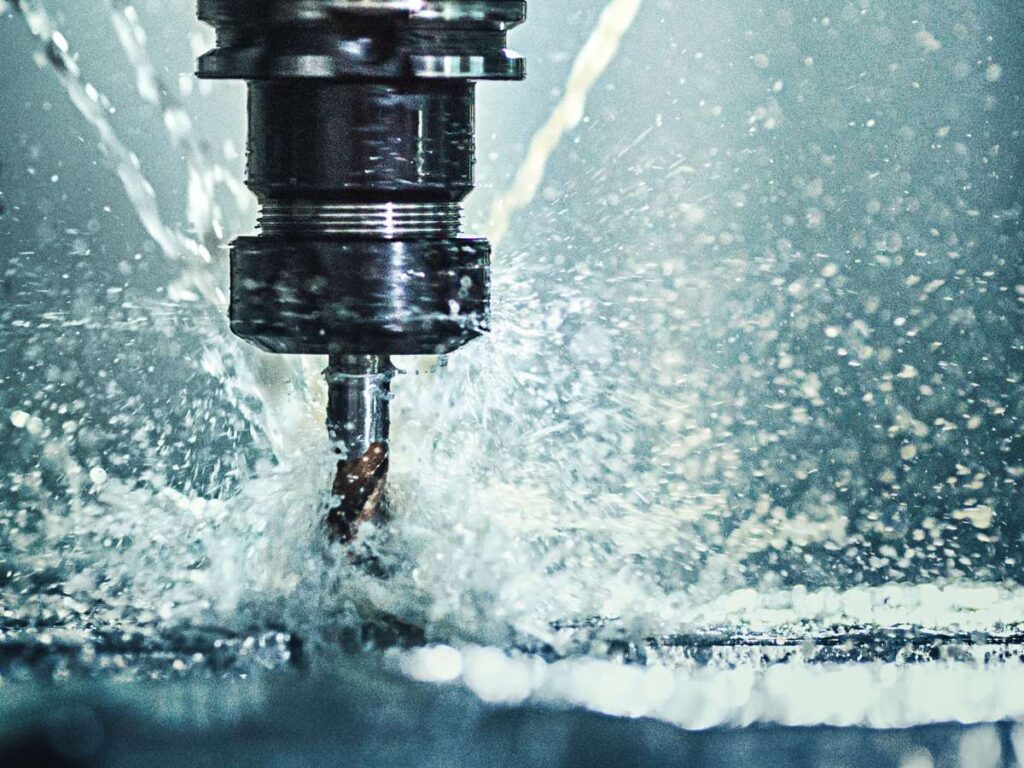
Conclusion
Choosing the right CNC machine isn’t just about specs but choosing the right tool to bring your ideas to life. Whether you need speed, precision, or power, there’s a CNC machine that fits your needs.
The question is: Are you ready to take the next step?
You’ve seen how different machines work. Now, it’s time to put that knowledge into action, don’t waste time on the wrong machine like I once did.
Let’s get started! Contact us today and find the CNC machine that moves your business forward.
Recommended Reads for You
Want to learn more? Here are some articles filled with valuable tips and information to guide you further:
- CNC Machine Definition
- CNC Machine Structure: Key Components Explained
- Exploring 10 Different Types of CNC Machines
Still haven’t found what you’re looking for? Don’t hesitate to contact us. We’re available around the clock to assist you.