I remember the first time I stood in front of a CNC machine. The hum of the spindle, the sharp precision of every cut—it was fascinating. But when it came time to program it, I realized I had no clue what I was doing.
If you’re new to CNC machining, you’ve probably felt the same way. The learning curve can be steep, and finding clear, no-nonsense answers is tough.
That’s why this guide exists. Backed by industry expertise and real-world experience, we’ve compiled answers to the most common CNC questions. No fluff, no jargon—just practical insights you can use.
You’ll learn how CNC machines work, the best ones for your business, and how to avoid costly mistakes. By the end, you’ll have the confidence to make smart decisions.
So, let’s get started!
1. How Do CNC Machines Work?
Imagine this: You design a part on your computer, hit a button, and a machine cuts, drills, or carves it with flawless precision. No wasted material. No human error. Just pure accuracy. That’s the power of CNC machining.
But let’s be real—understanding how a CNC machine works can feel overwhelming at first. The technical jargon, the programming, the endless moving parts. It’s a lot. But once you break it down, it all makes sense.
Step#1 It Starts With Digital Design
Before a CNC machine makes a single cut, it needs a plan. That plan comes from CAD (Computer-Aided Design) software.
This is where you create a blueprint—a 2D or 3D model of the part you need. Every dimension, shape, and feature is carefully mapped out. Think of it like a GPS for your CNC machine. Without clear instructions, it won’t know where to go.
Step#2 Converting the Design Into Machine Code
Once your design is ready, it needs to be translated into a language the CNC machine understands. This is where CAM (Computer-Aided Manufacturing) software steps in. CAM software generates G-code, a set of step-by-step instructions that tell the machine exactly what to do:
- Move the cutting tool
- Change spindle speeds
- Adjust feed rates
- Switch between tools
Step#3 The CNC Machine Does the Work
Now comes the exciting part. The CNC machine follows the programmed G-code, moving the cutting tool with extreme accuracy. Depending on the machine type, it might:
- Mill: Cutting away material to shape the part
- Turn: Spinning the workpiece to create cylindrical shapes
- Laser Cut: Using a high-powered laser for precision cuts
- Router: Cutting softer materials like wood or plastic
Unlike manual machining, CNC machines work with consistent accuracy, speed, and efficiency.
Step#4 Automation Means Higher Productivity
Let’s be honest—manual machining is time-consuming, inconsistent, and prone to human error. CNC machines eliminate those problems.
- Faster Production: Get more parts in less time
- Higher Accuracy: No more wasted material
- Scalability: Run the machine 24/7, increasing output
2. What Are the Different Types of CNC Machines?
CNC machines come in various types, each engineered for precision, efficiency, and specialized applications. Here’s a breakdown of the most commonly used CNC machines and what they are designed to do:
CNC Milling Machines
CNC mills are among the most versatile machining tools in modern manufacturing. They use rotary cutting tools to remove material from a workpiece, producing highly detailed and accurate parts. These machines can operate in multiple axes—typically 3 to 5—allowing for complex geometries and fine details.
- Best for: Metal and plastic parts requiring intricate shapes and precision drilling
- Industries: Aerospace, automotive, medical, and general manufacturing
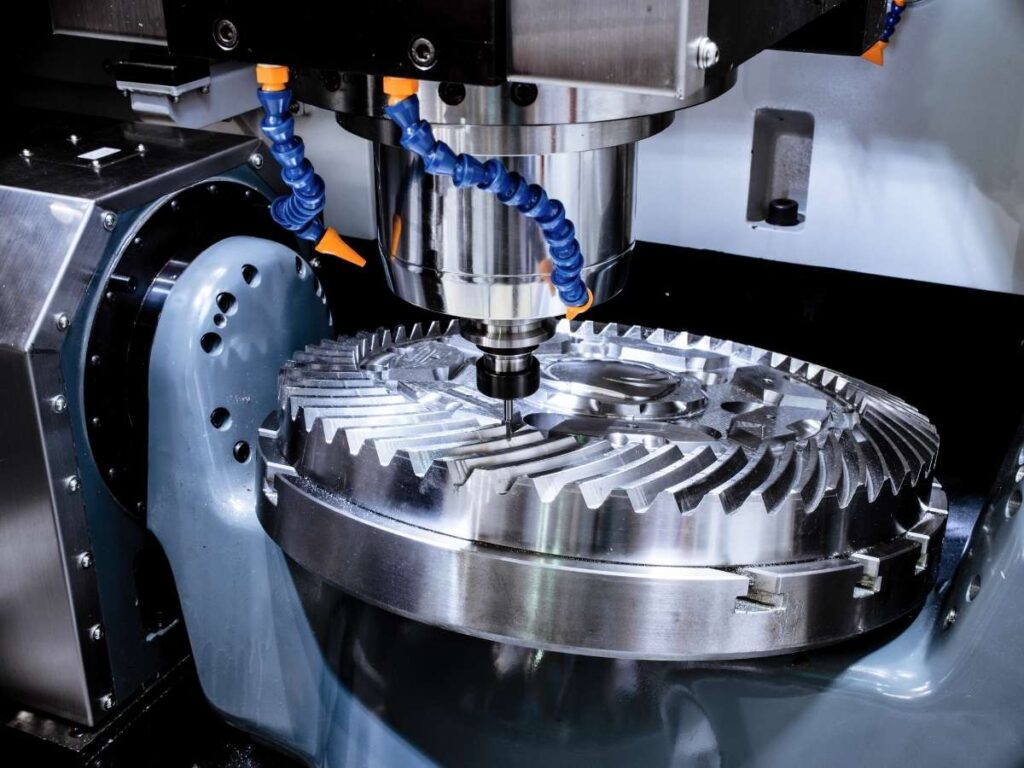
CNC Lathes
CNC lathes specialize in turning operations, where the workpiece rotates while a fixed cutting tool removes material. These machines are ideal for producing symmetrical parts such as shafts, bushings, and threaded components. Modern CNC lathes can include live tooling capabilities, allowing for milling, drilling, and tapping within the same machine.
- Best for: Round or cylindrical components requiring high accuracy
- Industries: Oil and gas, transportation, firearms, and industrial equipment
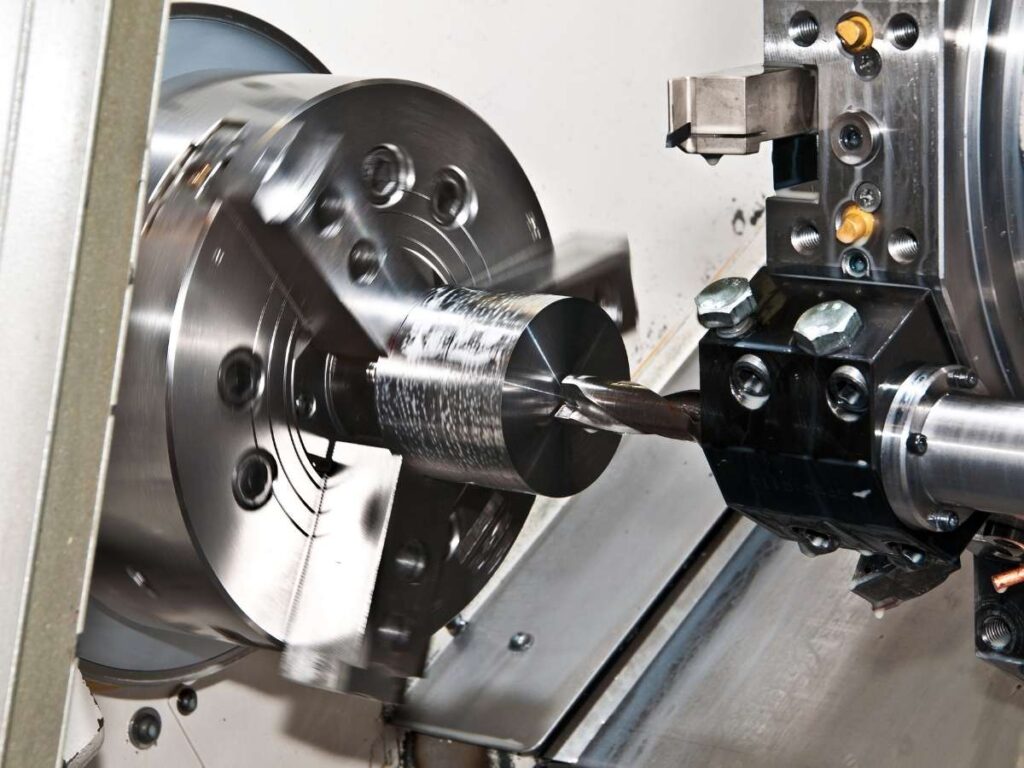
CNC Routers
CNC routers are optimized for high-speed cutting of wood, plastics, foam, and soft metals. They function similarly to CNC mills but are built for handling large sheets of material, making them invaluable in furniture production, sign-making, and prototyping.
- Best for: Large-scale woodwork, engraving, and lightweight material cutting
- Industries: Woodworking, signage, prototyping, and architectural modeling

CNC Plasma Cutters
CNC plasma cutters use a high-velocity jet of ionized gas to cut through metal with extreme accuracy and speed. These machines are best suited for cutting thick sheets of conductive materials, including steel, aluminum, and brass. Plasma cutting is faster and more cost-effective than traditional saw-cutting methods, making it a preferred choice for industrial applications.
- Best for: Cutting thick metal sheets with speed and precision
- Industries: Metal fabrication, automotive, shipbuilding, and construction
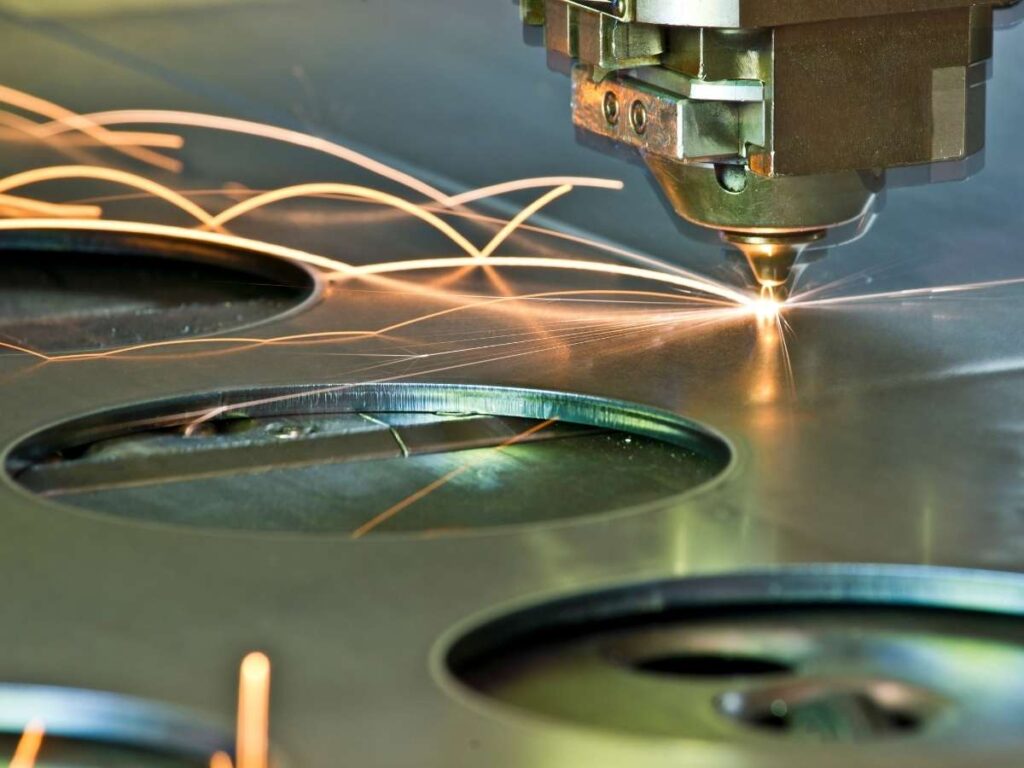
CNC Laser Cutters
CNC laser cutters use a focused laser beam to cut or engrave a variety of materials with microscopic precision. They excel in producing intricate designs, fine engravings, and smooth edges without requiring additional finishing. These machines can cut through metals, plastics, glass, and even fabrics with remarkable speed.
- Best for: Intricate engraving, precise cuts, and delicate materials
- Industries: Jewelry, electronics, packaging, and custom manufacturing
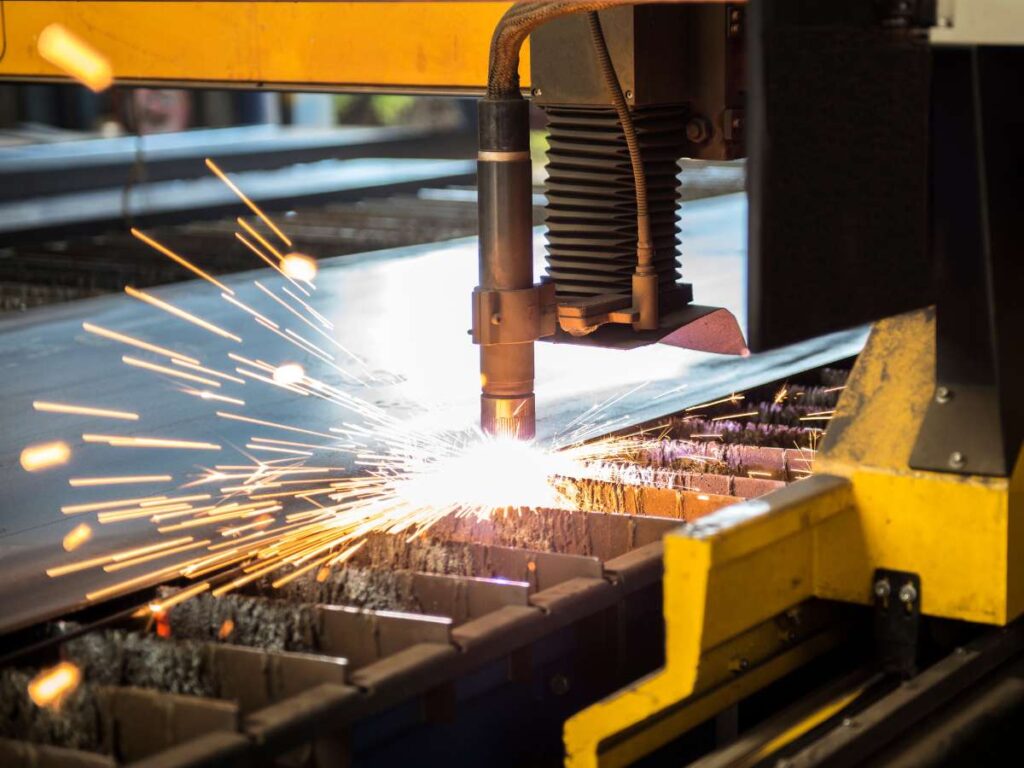
CNC Water Jet Cutters
CNC water jet cutters utilize a high-pressure stream of water—sometimes mixed with an abrasive material—to cut through virtually any substance. Unlike plasma and laser cutters, water jet cutting does not generate heat, preventing warping or material distortion. This makes it ideal for heat-sensitive materials and multi-layer cutting.
- Best for: Cutting thick materials without thermal damage
- Industries: Aerospace, stone and tile, metal fabrication, and food processing
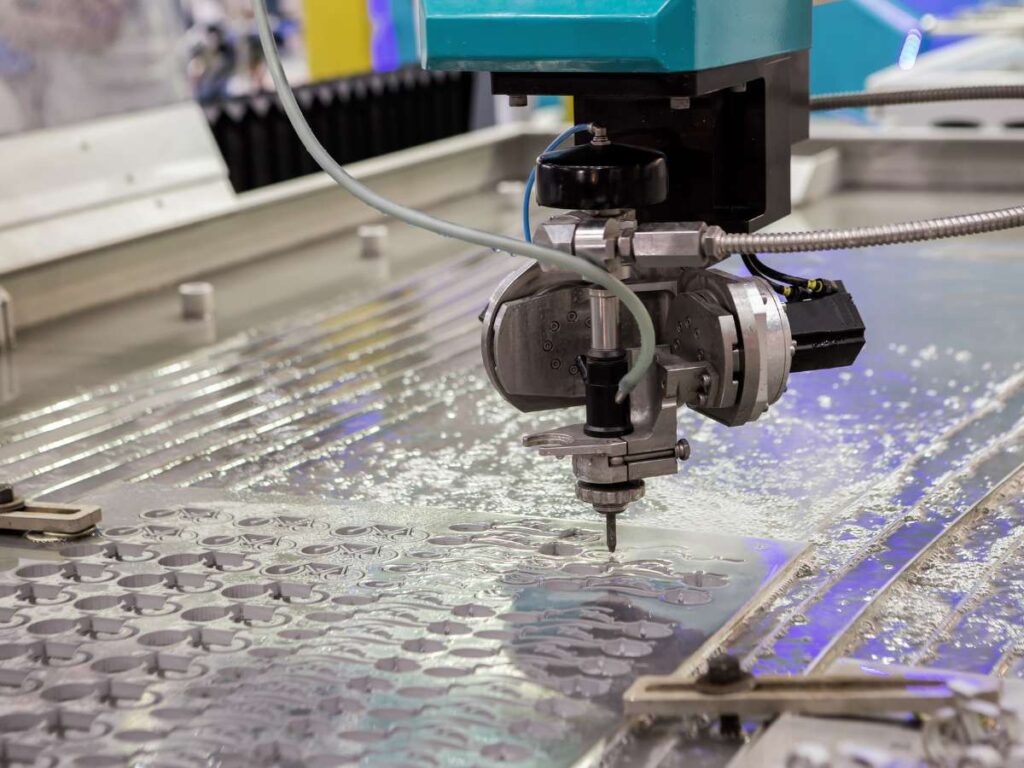
CNC Electrical Discharge Machines (EDM)
EDM, also known as spark machining, removes material using controlled electrical discharges. This process is ideal for hard metals and creating complex internal geometries that traditional cutting tools cannot achieve. EDM is commonly used for making molds, dies, and aerospace components requiring extreme precision.
- Best for: Hard-to-machine metals and intricate internal structures
- Industries: Aerospace, tool and die manufacturing, medical, and defense
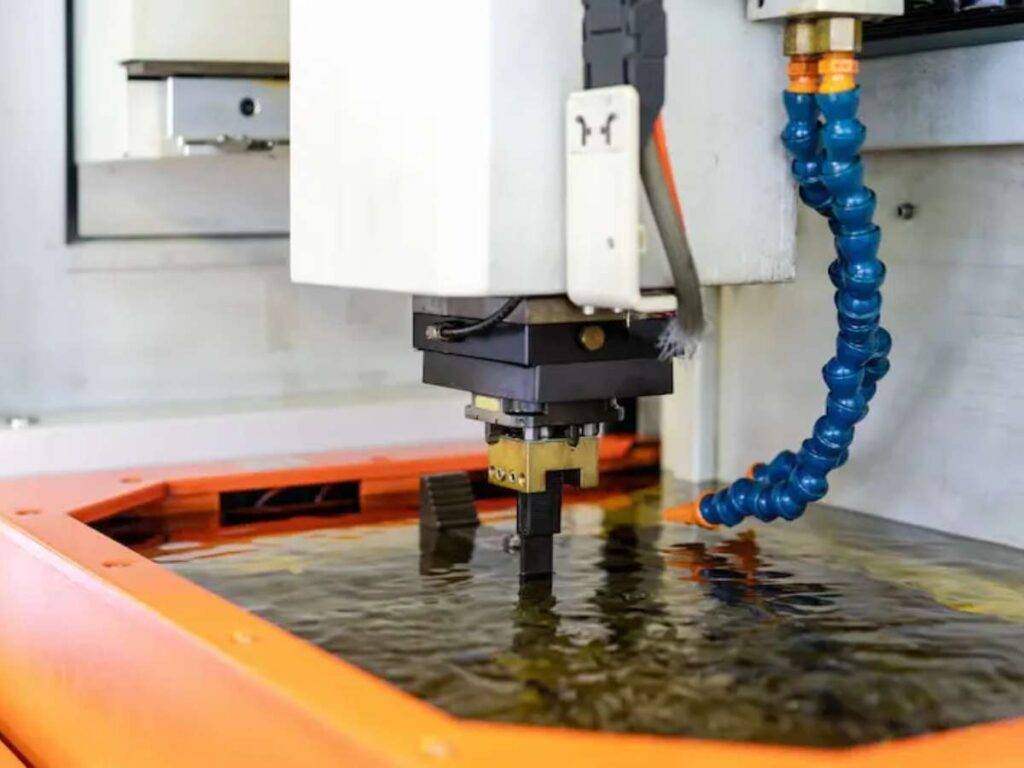
3. What Materials Can Be Used in CNC Machines?
The choice of material in CNC machining is just as critical as the machine itself. The right material impacts precision, durability, machining speed, and cost efficiency.
CNC machines are engineered to handle a vast range of materials, from metals to plastics, composites, and even wood. Understanding their properties helps businesses maximize performance and cost-effectiveness in production.
Metals
Metals are the backbone of CNC machining, valued for their strength, durability, and machinability. They are widely used in automotive, aerospace, medical, and industrial manufacturing.
- Aluminum: Lightweight, corrosion-resistant, and easy to machine. Ideal for aerospace, automotive, and electronics.
- Steel: High strength and wear resistance. Used for structural components, industrial machinery, and tooling.
- Stainless Steel: Corrosion-resistant with excellent strength. Common in medical devices, food processing equipment, and marine applications.
- Titanium: Extreme strength-to-weight ratio with high heat resistance. Essential for aerospace, military, and medical implants.
- Brass & Copper: Excellent for electrical conductivity and decorative applications. Used in electrical components, plumbing, and precision instruments.
Metals require robust cutting tools and precise control to achieve tight tolerances and high-quality surface finishes.
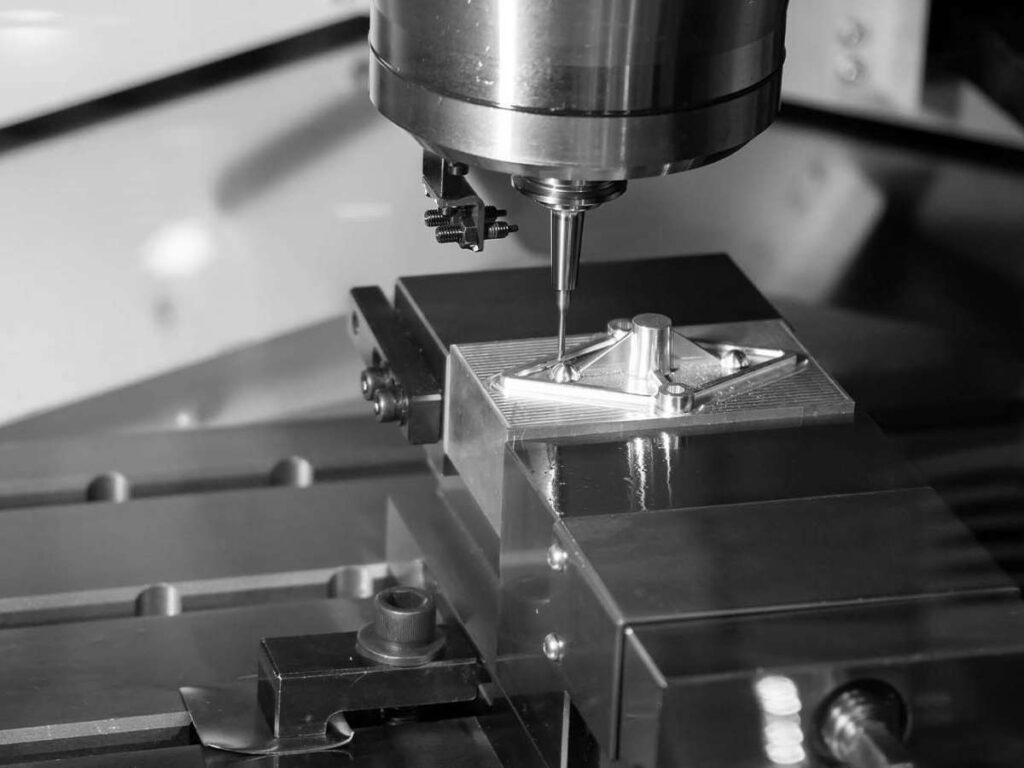
Plastics
Plastics are a cost-efficient alternative to metals and are widely used in consumer products, medical devices, and electronics. CNC machining allows for tight tolerances and complex geometries in plastic components.
- ABS: Strong, impact-resistant, and easy to machine. Used in automotive, medical, and consumer goods.
- Acrylic: Transparent, lightweight, and shatter-resistant. Common in display cases, lighting fixtures, and signage.
- Polycarbonate: High strength and heat resistance. Found in bulletproof glass, protective covers, and aerospace components.
- Nylon: High wear resistance and low friction. Used in gears, bearings, and mechanical components.
- PTFE (Teflon): Chemical-resistant and non-stick. Essential for medical, food processing, and aerospace industries.
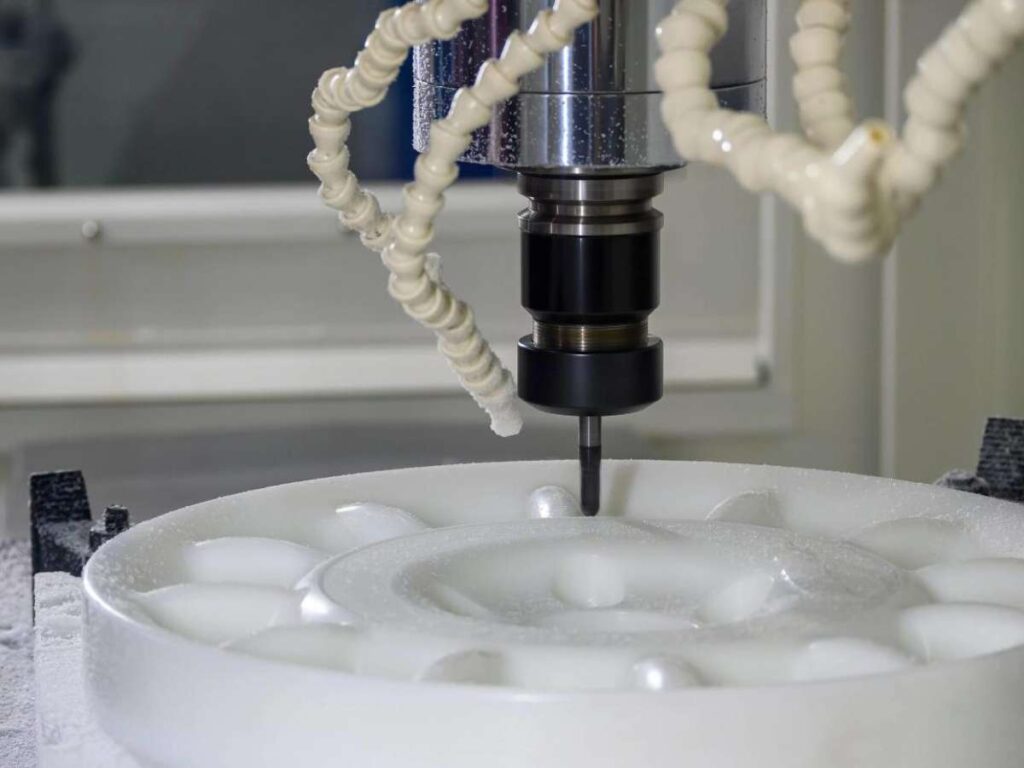
Composites
Composites combine multiple materials to achieve superior strength, weight reduction, and thermal stability. These materials are engineered for extreme performance and are commonly used in aerospace, automotive, and defense applications.
- Carbon Fiber: Extremely lightweight with high tensile strength. Used in aerospace, racing, and high-performance sporting goods.
- Fiberglass: Strong, lightweight, and corrosion-resistant. Ideal for marine, automotive, and industrial components.
- G10 & FR4: High-strength fiberglass laminates with electrical insulation properties. Used in circuit boards and structural parts.
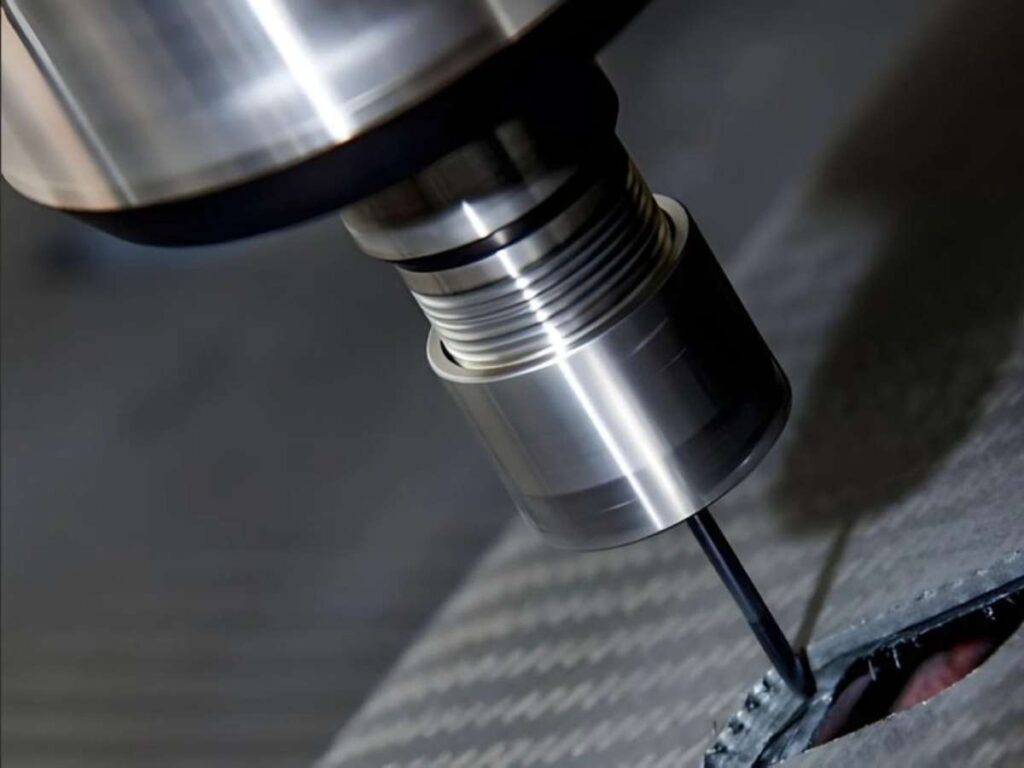
Wood
Though CNC machining is often associated with metals and plastics, it plays a significant role in woodworking, furniture production, and architectural design. CNC routers and mills efficiently cut, carve, and engrave wood for detailed, high-volume production.
- Hardwood (Oak, Maple, Walnut): Used for furniture, cabinetry, and decorative applications.
- Softwood (Pine, Cedar): Ideal for construction and lightweight designs.
- Plywood & MDF: Engineered wood materials used for mass production, signage, and furniture.
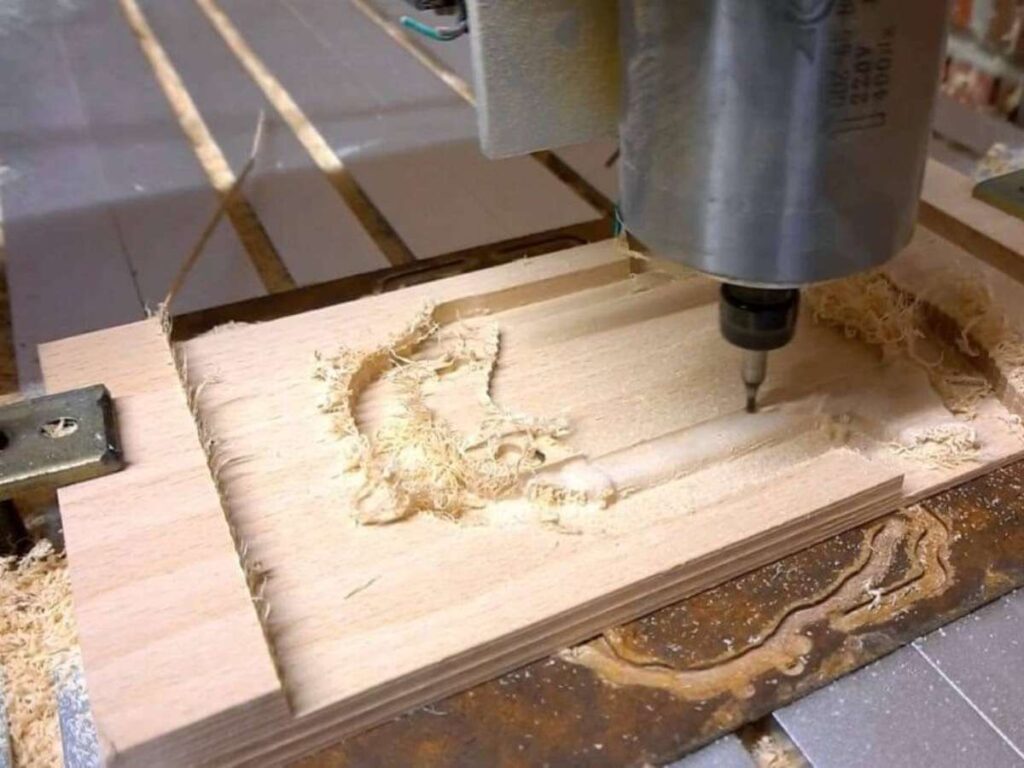
Foams & Soft Materials
CNC machines also process soft materials such as foams and rubber for applications that require shock absorption, insulation, or cushioning.
- Polyurethane Foam: Used for packaging, insulation, and lightweight prototypes.
- Expanded Polystyrene (EPS): Ideal for molds, props, and display models.
- Rubber & Silicone: Flexible materials used in seals, gaskets, and medical applications.
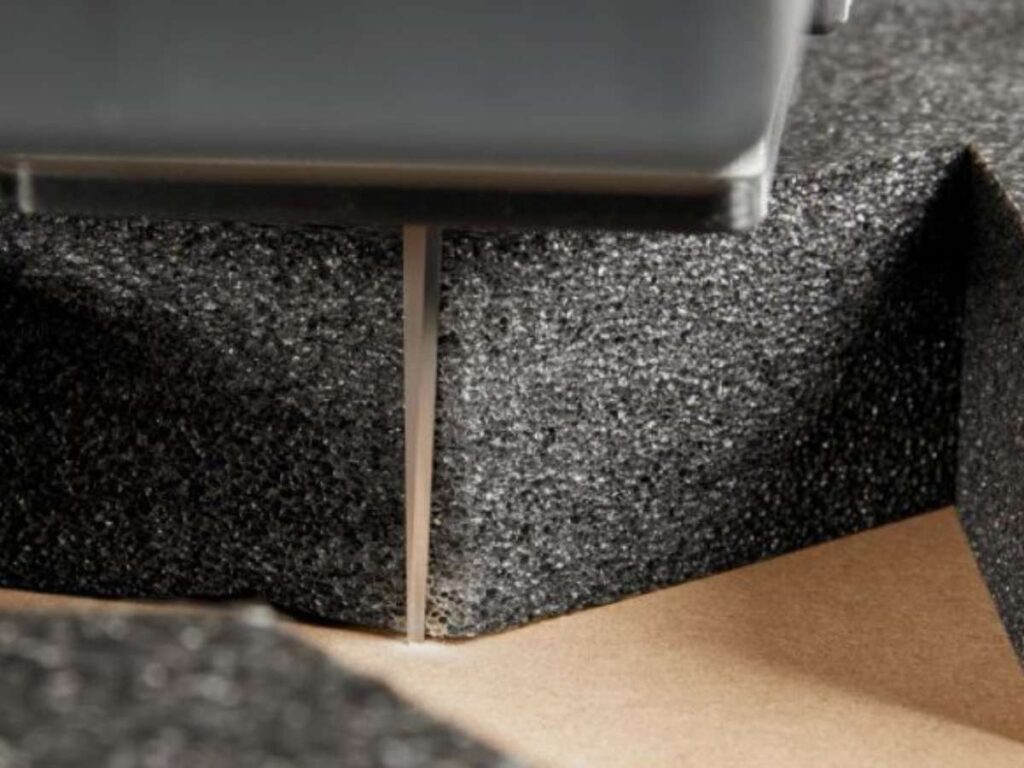
4. How Do You Program a CNC Machine?
The first time I tried to program a CNC machine, I was overwhelmed. The code looked like a foreign language, the software felt intimidating, and I wasn’t sure where to start. But after working through the process—trial, error, and eventually success—I realized something: CNC programming isn’t as complicated as it seems. It just needs structure and logic.
Learning to program it effectively can mean the difference between flawless parts and costly mistakes. Let’s break it down step by step:
Step#1 Designing the Part in CAD Software
Before the CNC machine can do anything, it needs a blueprint. That’s where CAD (Computer-Aided Design) software comes in. This is where you create the exact shape, dimensions, and features of the part you want to machine. Some of the most commonly used CAD programs include:
- AutoCAD: Ideal for precise 2D and 3D modeling
- Fusion 360: Perfect for small businesses and prototyping
- SolidWorks: Industry-standard for complex mechanical parts
- Rhino: Great for intricate and artistic designs
At this stage, every hole, cut, and surface finish is defined. A well-designed CAD model ensures a smoother programming process.
Step#2 Converting the Design into G-Code
Once the design is ready, it needs to be translated into instructions the CNC machine can execute. This is done using CAM (Computer-Aided Manufacturing) software.
CAM software converts the design into G-code, the programming language that controls the machine. This code tells the machine where to move, how fast to move, and when to cut. Popular CAM software includes:
- Mastercam: Powerful tool for industrial CNC machining
- Fusion 360 CAM: Ideal for small shops and startups
- GibbsCAM: Used for complex multi-axis machining
Every command in G-code follows a simple structure:
- G00 (Rapid Movement): Moves the tool quickly to a location without cutting
- G01 (Linear Cutting Movement): Moves the tool in a straight line while cutting
- G02/G03 (Circular Cutting): Moves the tool in arcs or circles
- M06 (Tool Change): Changes to a different cutting tool
Step#3 Setting Up the CNC Machine
Once the G-code is generated, it’s time to set up the CNC machine. Even the best program won’t work if the machine isn’t configured correctly. This step includes:
- Selecting the Right Cutting Tool: Different tools for drilling, milling, and engraving
- Securing the Workpiece: Using vises, clamps, or vacuum fixtures to hold the material in place
- Setting the Zero Point: Establishing the starting position (also called the work offset) so the machine knows where to begin cutting
Step#4 Running a Test Simulation
Before running the program on the actual material, always perform a test run (also called a dry run).
Why? Because even the smallest programming mistake can cause tool breakage, machine damage, or scrapped parts. How? Most CAM software includes simulation tools that visually show how the machine will move.
A test run ensures that the tool paths are correct, the machine won’t crash, and the final product matches the design.
Step#5 Executing the Program and Monitoring the Process
Once everything checks out, it’s time to run the CNC machine. The machine follows the programmed instructions, cutting and shaping the material with extreme precision.
But programming doesn’t stop once the machine starts running. Constant monitoring is required to:
- Check for errors
- Watch for tool wear
- Ensure consistency
A well-programmed CNC machine delivers repeatability, speed, and efficiency, but only when programmed correctly.
5. What Are the Most Common Mistakes Beginners Make?
CNC machining is precise, powerful, and transformative—but it’s also unforgiving. A single mistake can mean wasted material, broken tools, or even machine damage.
When I first started, I made errors that cost time, money, and frustration. But those mistakes became lessons, and now, I see the same patterns repeated by beginners.
If you’re new to CNC machining, you don’t have to learn the hard way. Here are the most common mistakes beginners make—and how to avoid them:
Incorrect Tool Selection
CNC machining is all about precision, and using the wrong tool can lead to poor cuts, tool breakage, and wasted material. Many beginners assume any tool will work, but that’s a costly assumption.
- Milling vs. Drilling Tools: End mills are for cutting sideways; drill bits are for plunging. Mixing them up leads to bad cuts and broken bits.
- Wrong Tool Material: Carbide tools last longer for metals, while high-speed steel (HSS) works better for softer materials.
- Ignoring Coatings: Some tools have coatings that increase wear resistance—choosing the wrong one means faster tool degradation.
Solution: Always match the tool to the material and operation. Check speed ratings, flute types, and coatings before running a job.
Incorrect Feeds and Speeds
The wrong combination of feed rate (how fast the tool moves) and spindle speed (how fast it spins) can destroy both your workpiece and your tool.
- Too Fast? You’ll burn out your tool, create rough finishes, or cause excessive heat buildup.
- Too Slow? The tool may rub instead of cutting, leading to dull edges and wasted machining time.
- Wrong Depth of Cut? Taking off too much material in one pass overloads the tool and the machine.
Solution: Use manufacturer-recommended settings for feed rates and spindle speeds. Start conservative, then adjust as needed.
Poor Workholding
Imagine setting up a perfect CNC program, only to have your workpiece shift mid-cut. Disaster. Improper clamping leads to misalignment, inaccurate cuts, and dangerous machine crashes.
- Clamps Too Loose? The material shifts, ruining the cut.
- Clamps Too Tight? It can damage soft materials or deform thin parts.
- Ignoring Workholding Methods? Some cuts require vises, vacuum tables, or custom fixtures to keep the workpiece stable.
Solution: Always test your setup before running a job. Apply even pressure and make sure the workpiece won’t move under cutting forces.
Skipping the Tool Zeroing Process
If the tool doesn’t start from the correct zero point, every cut will be off. Beginners often assume the machine knows where the workpiece is—but CNC machines only follow instructions. If zero is wrong, the entire job is wrong.
- Wrong Work Offsets? The machine cuts in the wrong place.
- Tool Not Touched Off Correctly? The depth of the cut is too shallow or too deep.
- Forgetting to Set Multiple Tool Offsets? When using multiple tools, each one needs its own zeroing.
Solution: Always zero the tool properly before running a job. Double-check offsets before pressing start.
6. What Safety Measures Should I Follow?
CNC machines are powerful, precise, and essential for modern manufacturing. But they can also be dangerous if handled carelessly. One moment of inattention, a skipped safety step, or improper machine use can lead to costly damage.
If you’re operating CNC machines, safety isn’t an option—it’s a requirement. Whether you’re running a small shop or managing a large-scale production line, these essential safety measures will protect both your operators and your equipment.
Wear Proper Personal Protective Equipment (PPE)
CNC machines generate high-speed rotating tools, flying debris, and loud noise. Wearing the right PPE is the first line of defense against accidents.
- Safety Glasses or Face Shields: Protect against flying chips and coolant splashes.
- Hearing Protection: CNC machines can be loud, leading to long-term hearing damage. Use earplugs or earmuffs.
- Protective Gloves (Only When Not Operating the Machine): Avoid loose-fitting gloves near rotating tools, but wear cut-resistant gloves when handling sharp materials.
- Steel-Toe Boots: Protect feet from heavy falling objects or dropped tools.
- Fire-Resistant Clothing: Avoid synthetic fabrics that can melt onto the skin in case of heat exposure.
Secure the Workpiece and Tools Properly
A loose workpiece is a disaster waiting to happen. If a part shifts during machining, it can cause tool breakage, machine damage, or even send sharp material flying.
- Use Proper Workholding Methods: Clamps, vises, vacuum fixtures, or custom jigs keep the material in place.
- Double-Check Tool Tightness: Loose tools can break and become dangerous projectiles.
- Never Over-Tighten Fixtures: Over-clamping can deform softer materials like plastic or aluminum.
Never Leave a Running CNC Machine Unattended
It might be tempting to step away and let the machine do its job, but that’s one of the most dangerous habits. A single error can lead to tool crashes, fire hazards, or major production failures.
- Monitor the First Few Runs: The initial passes confirm if the program is running correctly.
- Watch for Abnormal Noises: Unusual sounds can indicate tool wear, incorrect feed rates, or workpiece movement.
- Stay Close to the Emergency Stop (E-Stop) Button: If something goes wrong, stopping the machine immediately can prevent bigger problems.
Understand and Follow Lockout
CNC machines require high-voltage power, hydraulic pressure, and mechanical motion—which means they can be deadly if serviced incorrectly. Lockout/tagout (LOTO) procedures prevent accidental machine startups during maintenance.
- Always Power Down Before Maintenance: Turn off electrical, pneumatic, or hydraulic power before performing any work.
- Use Lockout Devices: Lock the power switch in the OFF position to prevent unauthorized restarts.
- Tag Machines with Warnings: Clearly indicate when a machine is being serviced.
Regularly Inspect the CNC Machine
A poorly maintained CNC machine is not only inefficient—it’s dangerous. Small issues like worn-out bearings, dull cutting tools, or misaligned spindles can quickly lead to catastrophic failures.
- Inspect Cutting Tools Regularly: Dull tools create excessive heat and can break under pressure.
- Check for Loose Bolts or Fasteners: Vibrations can loosen components over time.
- Lubricate Moving Parts: Friction can cause overheating and premature wear.
- Test Emergency Stop and Safety Guards: Ensure that all safety features are functioning before operation.
7. How Much Does a CNC Machine Cost?
Investing in a CNC machine isn’t just about buying equipment—it’s about making a strategic decision that affects production efficiency, scalability, and profitability. CNC machines range from a few thousand dollars to hundreds of thousands, depending on factors.
Understanding the cost structure will help you make an informed decision based on your business needs. Let’s break down the pricing and key factors that influence it:
CNC Machine Price Ranges
CNC machine costs vary widely based on their type, complexity, and application. Here’s a general pricing breakdown:
- Entry-Level CNC Machines ($2,000 – $10,000)
- Small benchtop mills, routers, and hobbyist CNC machines
- Limited capabilities, lower precision, and slower speeds
- Ideal for small businesses, prototyping, and light materials
- Mid-Range CNC Machines ($10,000 – $100,000)
- Industrial-grade CNC mills, lathes, and routers
- Capable of machining metals, plastics, and composites
- Suitable for small to mid-sized manufacturing operations
- High-End CNC Machines ($100,000 – $500,000+)
- Advanced 5-axis machining centers and high-precision systems
- Fully automated, high-speed, multi-tool capabilities
- Designed for aerospace, automotive, medical, and large-scale production
Factors That Affect CNC Machine Cost
The final cost of a CNC machine depends on several critical factors:
- Machine Type and Complexity: A 3-axis CNC mill is far cheaper than a 5-axis machining center. Lathes, routers, plasma cutters, and laser cutters each have unique pricing structures.
- Machine Size and Work Envelope: Larger machines with bigger work envelopes cost more but offer greater versatility. Compact CNC machines are cheaper but limit the size of parts you can produce.
- Automation and Software Integration: Fully automated CNC machines with robotic loading systems are more expensive but significantly improve efficiency. Advanced CAD/CAM software integration increases programming ease but adds to the overall cost.
- Material Capability: Machines designed to cut soft materials like wood and plastic are cheaper. High-rigidity machines for titanium, stainless steel, and aerospace-grade alloys are significantly more expensive.
- Precision and Tolerance Requirements: Standard CNC machines can achieve tolerances of ±0.01mm, while ultra-precision machines reach ±0.001mm. Higher precision requires rigid construction, advanced controllers, and better tooling, which increases cost.
- Brand, Manufacturer, and Country of Origin: Well-known brands like Haas, Mazak, DMG Mori, and Okuma come at a premium but offer superior reliability. Lower-cost machines from China like in Blue Elephant are more affordable but may require modifications or higher maintenance.
8. What Maintenance is Required for a CNC Machine?
A CNC machine is an investment, and like any precision tool, it demands regular maintenance to deliver peak performance. Neglecting maintenance leads to machine downtime and costly repairs. Let’s break down the essential CNC maintenance tasks you must perform to protect your investment:
- Daily Maintenance: A few minutes of daily maintenance can prevent hours of lost production time. Every operator should follow these simple yet crucial steps at the start and end of every shift.
- Clean the Machine and Work Area
- Check Lubrication Levels
- Inspect Cutting Tools
- Check for Loose Bolts or Fasteners
- Monitor Coolant Levels and Quality
- Run a Warm-Up Cycle
- Listen to Unusual Noises
- Weekly Maintenance: Once a week, operators should take a deeper look at key systems to catch early signs of wear and tear.
- Inspect and Clean Spindle and Tool Holders
- Check the Air Supply System
- Test Emergency Stop and Safety Features
- Flush and Refill Coolant Reservoirs
- Check Belt Tension and Drive Systems
- Monthly Maintenance: Monthly maintenance involves detailed inspections to ensure the CNC machine remains in optimal condition for long-term use. This step helps prevent breakdowns that can halt production and lead to costly repairs.
- Check Spindle Runout and Alignment
- Inspect Linear Rails and Bearings
- Verify Machine Leveling
- Calibrate Axes and Check Backlash
- Check Electrical Connections
- Annual Maintenance: A full annual maintenance check-up ensures the machine remains in peak condition and prevents long-term failures.
- Complete Spindle and Bearing Inspection
- Inspect Hydraulic and Pneumatic Systems
- Test and Update Software and Firmware
- Recalibrate the Entire Machine
- Conduct a Full Safety Audit
9. What Are the Best CNC Machines for Beginners?
Choosing the right CNC machine as a beginner can be challenging. It’s essential to find a machine that balances affordability, ease of use, and capability without compromising quality. Here are some top recommendations:
Blue Elephant 1325 4x8ft 3 Axis CNC Wood Router
- Price: Approximately $5,000 – $8,000
- Best For: Woodworking, cabinetry, and sign-making
- Features:
- Generous working area of 1300x2500mm, ideal for large panels
- Equipped with a 4.5kW air-cooled spindle for efficient cutting
- User-friendly DSP A11 control system, suitable for beginners
- Durable construction ensures long-term reliability
Why It’s Great for Beginners: The Blue Elephant 1325 offers a spacious work area and robust features at an accessible price point, making it ideal for those new to CNC woodworking.
Tormach 1100MX
- Price: $15,000 – $20,000
- Best For: Small businesses, prototyping, and custom machining
- Features:
- Easy-to-use PathPilot® control system
- Handles materials like aluminum, steel, and plastics
- Upgradeable with automatic tool changers and enclosures
Why It’s Great for Beginners: Tormach is known for affordable, industrial-grade CNC mills with excellent support and training materials.
Shapeoko 5 Pro
- Price: $2,000 – $3,500
- Best For: Woodworking, sign-making, and light prototyping
- Features:
- Large work area for cutting bigger materials
- Compatible with wood, plastics, and aluminum
- Carbide Create software simplifies programming
Why It’s Great for Beginners: Simple to use, affordable, and excellent for custom wood and plastic fabrication.
X-Carve by Inventables
- Price: $2,500 – $4,000
- Best For: DIY projects, crafts, and small business production
- Features:
- Plug-and-play setup with Easel software
- Ideal for sign-making, engraving, and woodworking
- Large cutting area accommodates oversized materials
Why It’s Great for Beginners: Comes with an intuitive online design platform that eliminates complex coding.
Genmitsu 3018-PRO
- Price: $300 – $600
- Best For: Learning CNC basics and small engraving jobs
- Features:
- Compact design suitable for engraving wood, acrylic, and soft materials
- Easy assembly with beginner-friendly software
- Affordable entry point for CNC enthusiasts
Why It’s Great for Beginners: A low-cost way to learn CNC programming and machine operation.
Conclusion
I started confused, made mistakes, and lost time and money. But with the right knowledge, I turned CNC into an asset instead of a challenge. Now, you have that knowledge too.
This guide covered everything from machine types to programming basics. The next step? Apply it. The sooner you start, the sooner you see results.
CNC isn’t just a machine—it’s a game-changer for your business.
What’s stopping you from making the most of it?
Let’s take your CNC journey to the next level.
Contact us today and let’s make CNC work for you!
More Guides and Tips to Explore
Want to see more? We’ve gathered additional product choices to give you even more variety:
Curious for more? These additional articles offer even more insights and advice:
General Knowledge
Advanced Topics & Forums
- Top 3 Largest CNC Machines in the World
- Retrofit CNC Machines: The Complete Guide
- Retrofit CNC Controller: The Ultimate Guide
- Top 8 Hobby CNC Forums
Still haven’t found what you’re looking for? Don’t hesitate to contact us. We’re available around the clock to assist you.