Back when I ran a small workshop, I did everything by hand. Every cut, every hole, every finish—it was slow and exhausting. If I needed a complex part, I had to measure, mark, and cut manually, hoping I wouldn’t make a mistake.
Then I got my first CNC machining center. It changed everything. I could take on more jobs, improve my quality, and finally compete with bigger shops.
If you’ve been relying on manual work or outdated machines, you might be wondering: Is a CNC machining center really worth it? I had the same question.
By the end of this article, you’ll know exactly what a CNC machining center is, what it does, and whether it’s the right fit for you.
Let’s dive in!
1. What is a CNC Machining Center?
If you’ve ever worked with traditional machining, you know how time-consuming and precise the process must be. Every cut, every measurement, and every adjustment takes effort. That’s where a CNC machining center changes everything.
Definition & Purpose
A CNC (Computer Numerical Control) machining center is an advanced, automated machine designed for precision cutting, drilling, milling, and shaping of materials. Instead of manual operation, it follows pre-programmed instructions to create parts efficiently and accurately.
Think of it as a highly skilled machinist—except it doesn’t get tired, doesn’t make mistakes from fatigue, and can run continuously.
How Does It Work?
A CNC machining center operates using:
- Pre-Programmed Software: Instructions are written in G-code, telling the machine where and how to move.
- Multi-Axis Movement: Most machines operate on at least three axes (X, Y, and Z), but advanced models can have up to five or more for complex parts.
- Automated Tool Changes: The machine switches between cutting tools without human intervention, reducing downtime.
Why Are They Used?
Businesses invest in CNC machining centers because they:
- Increase Efficiency: Machines work faster than manual operators.
- Improve Accuracy: Tolerances can be as tight as ±0.001 inches.
- Reduce Material Waste: Optimized cutting paths make the most of raw materials.
- Lower Labor Costs: One operator can oversee multiple machines.
Is a CNC Machining Center Right for You?
If you’re in manufacturing, metal fabrication, or custom machining, a CNC machining center can improve your production. But is it the right investment for your business?
- Do you handle high-volume production?
- Are you struggling with inconsistent quality or slow turnaround times?
- Would automation help you take on bigger or more complex jobs?
If you answered yes to any of these, then a CNC machining center might be the solution. And if you are looking for the best supplier, choose Blue Elephant. We tailor machines to your specifications and offer sample testing.
2. Advantages of Using CNC Machining Center
When I first transitioned from manual machining to a CNC machining center, I wasn’t convinced it was the right move. Would it really be faster? Would it improve my quality? Would it be worth the investment?
It didn’t take long to see the difference. Suddenly, jobs that used to take days were completed in hours. Parts were more precise, and I could take on more work without increasing labor. If you’re considering a CNC machining center, here’s why it might be the best decision for your business.
Precision and Consistency
One of the biggest advantages of CNC machining centers is their ability to produce identical parts with extreme accuracy.
- High Precision: CNC machining centers can achieve tolerances as tight as ±0.001 inches, eliminating human error.
- Consistent Quality: Every part produced matches the last, no matter how many are made.
- Advanced Programming: Pre-set software controls the entire process, reducing manual adjustments.
Have you ever scrapped a batch of parts because of small inconsistencies? With CNC machining, that problem disappears.
Versatility in Machining Operations
A CNC machining center can handle multiple machining tasks, replacing several standalone machines.
- Milling, Drilling, and Tapping: All in one setup.
- Multi-Material Capability: Works with metals, plastics, composites, and more.
- Customization: Can be programmed for different part designs with ease.
Need to switch from a metal part to a plastic one? No problem. Just load a new program, and the machine handles the rest.
Better Workflow and Less Downtime
Machine downtime costs businesses thousands of dollars. CNC machining centers minimize interruptions.
- Automated Operations: No waiting for manual adjustments.
- Predictable Maintenance: Routine servicing prevents unexpected failures.
- Quick Setup Changes: Load a new program and start machining right away.
How much time do you lose setting up jobs manually? CNC machining centers streamline the process, keeping production moving.
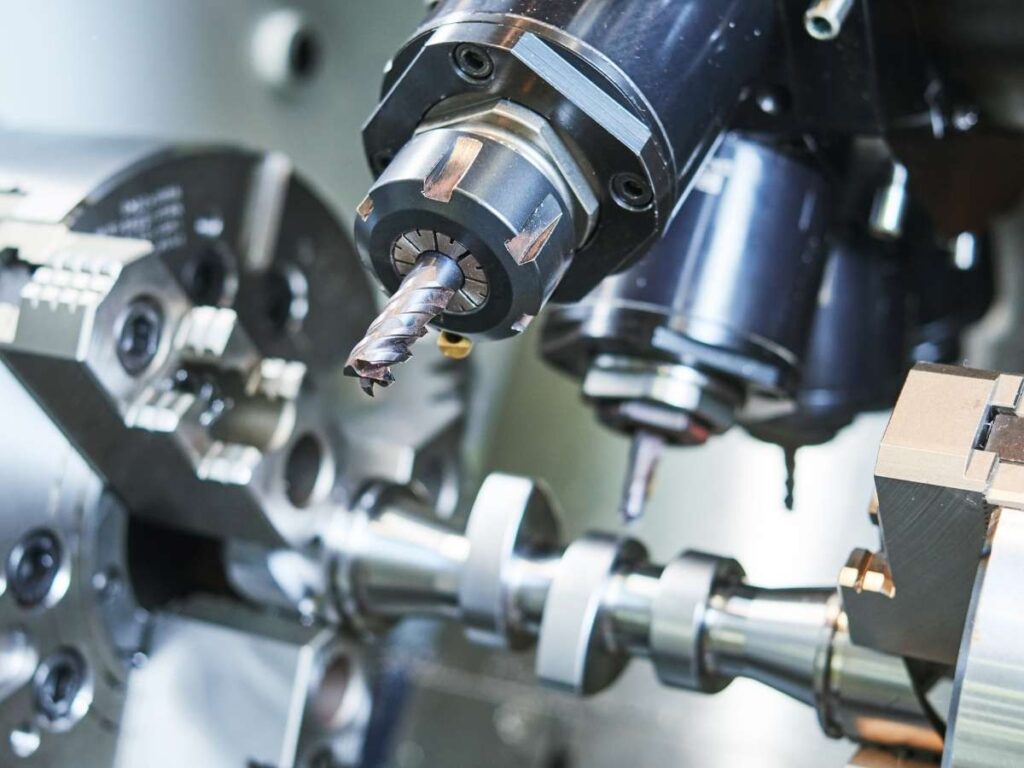
3. Types of CNC Machining Centers
Not all CNC machining centers are the same. Each type is designed for specific tasks, materials, and industries. Choosing the right one depends on what you need to machine, how precise you need to be, and how efficiently you want to work.
Let’s break down the most common types and where they fit best.
Vertical Machining Centers (VMC)
The first CNC machine I ever used was a vertical machining center (VMC). At the time, I didn’t know much about it, but I quickly realized why these machines are so popular.
Why Choose a VMC?
- Best for Flat Surfaces: The spindle is positioned vertically, making it ideal for machining flat parts.
- Great for Drilling & Die-Sinking: Handles hole-making and cavity cutting with precision.
- User-Friendly: Easier to program and operate than horizontal models.
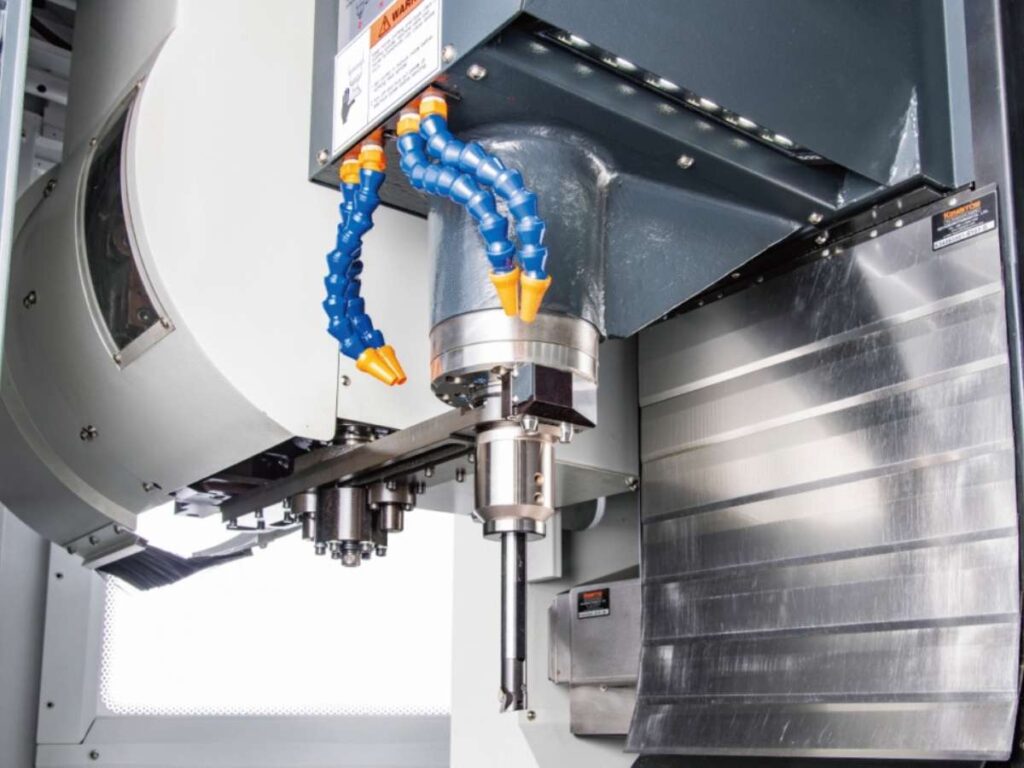
Horizontal Machining Centers (HMC)
I remember the first time I saw an HMC in action. The difference in chip removal alone was enough to make me reconsider my entire workflow.
Why Choose an HMC?
- Ideal for Deep Cavity Cutting: The horizontal spindle allows for better access to deeper areas.
- Higher Chip Removal Efficiency: Gravity helps chips fall away naturally, reducing heat buildup and tool wear.
- More Stable Machining: The workpiece is secured more rigidly, allowing for heavy cutting.
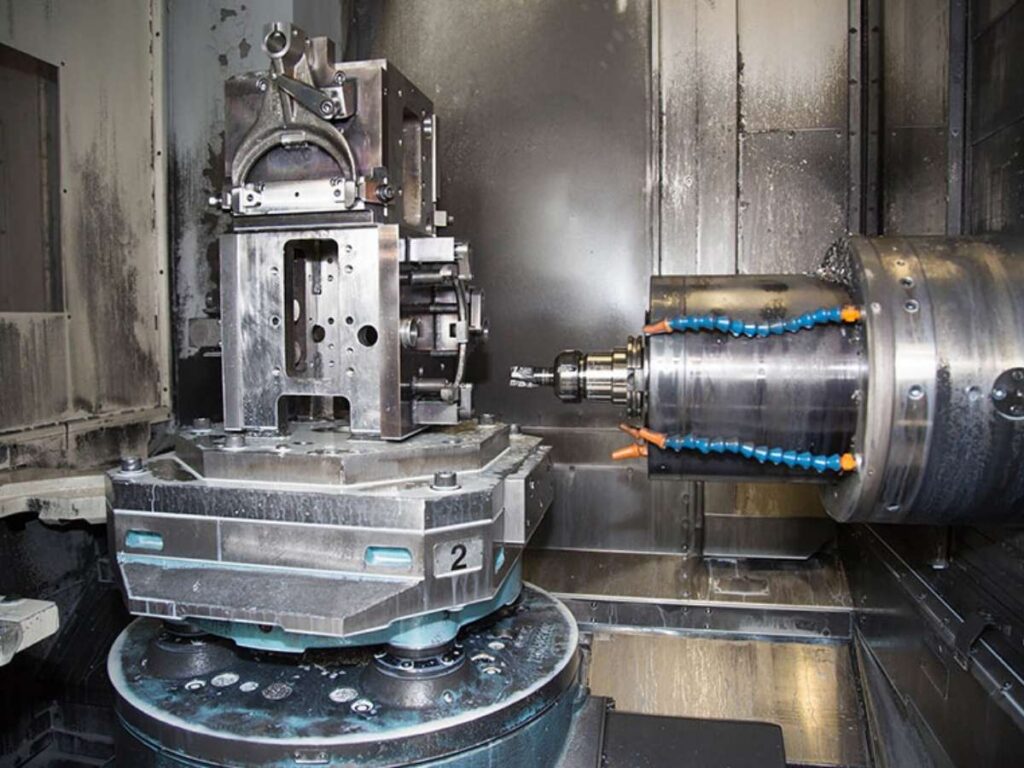
5-Axis Machining Centers
When I first worked with a 5-axis machining center, it felt like something out of science fiction. Suddenly, I could machine parts that would’ve been impossible with a standard 3-axis machine.
Why Choose a 5-Axis Machine?
- Enables Complex Shapes: Moves along five axes (X, Y, Z, A, and B) for intricate cuts.
- Fewer Setups: Reduces repositioning, which improves accuracy.
- Higher Precision: Ideal for parts requiring multiple angles and contoured surfaces.
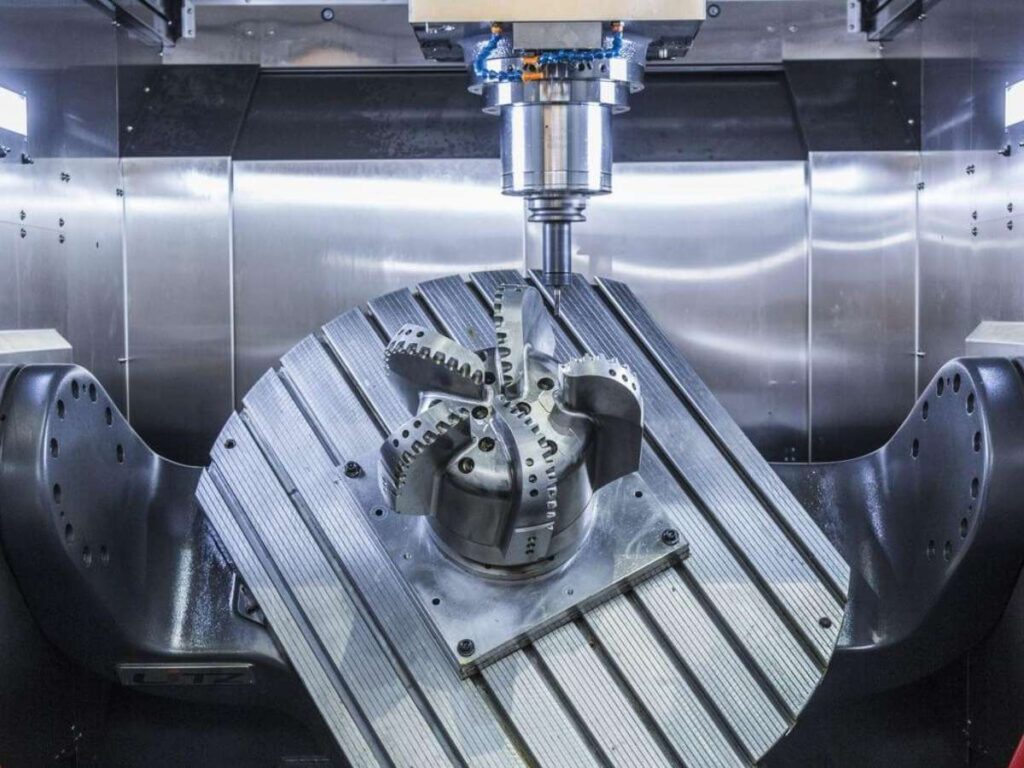
Universal Machining Centers
At some point, I found myself needing both vertical and horizontal machining capabilities. That’s when I discovered universal machining centers—machines that could do both.
Why Choose a Universal Machining Center?
- Handles Both Vertical & Horizontal Operations: The spindle rotates, allowing for multi-directional machining.
- Multi-Functional: Eliminates the need for separate machines.
- Reduces Setup Time: You don’t have to reposition the part as often.
The right machine can increase efficiency, improve accuracy, and reduce setup times. So, which one fits your business best?
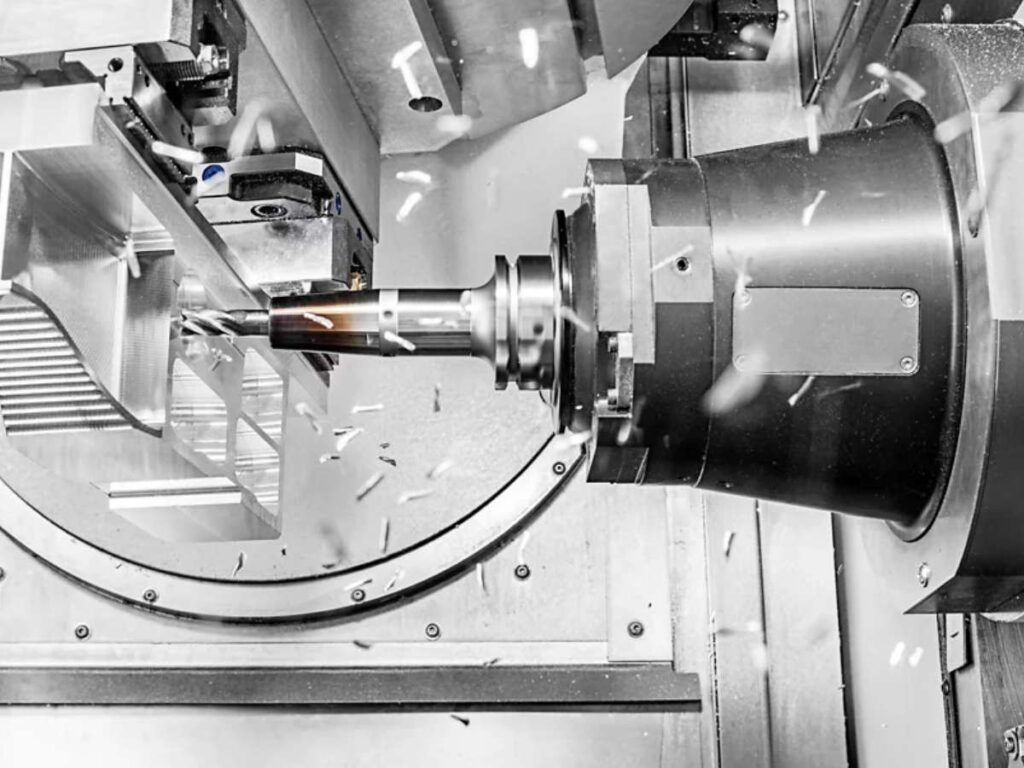
4. Key Features of CNC Machining Centers
Whether you’re sourcing CNC machining services or planning to invest in a machine, knowing what to look for can make all the difference. But what features truly impact performance, precision, and productivity? Let’s walk through the core components and functions that define a quality CNC machining center.
High Precision and Repeatability
CNC machining centers are built for tight tolerances and repeatable results—especially important for industries like aerospace, automotive, and medical. These machines often achieve accuracy within microns, thanks to advanced servo motors, rigid structures, and feedback systems.
Multi-Axis Capability
Standard machining centers operate on three axes (X, Y, Z). Advanced models offer 4-axis or 5-axis capabilities, allowing the tool to move in more directions. This increases flexibility and reduces the need for multiple setups.
- 3-Axis: Ideal for basic milling and drilling.
- 4-Axis: Adds rotary motion for more complex contours.
- 5-Axis: Allows full tool movement around the workpiece—great for complex geometries.
Automatic Tool Changer (ATC)
ATC systems allow the machine to switch between tools automatically during the machining cycle. This speeds up production and reduces manual intervention, especially when machining parts with multiple features.
If you’re producing small batches or need fast transitions between jobs, an ATC saves time and reduces human error.
User-Friendly CNC Controls
The machine’s control panel is where operators input programs and make adjustments. Modern controls offer intuitive interfaces, touchscreen displays, and compatibility with CAD/CAM software.
Look for:
- Clear interface navigation
- Built-in diagnostics
- Remote monitoring capabilities
5. Applications of CNC Machining Centers Across Industries
Industries that rely on CNC machining centers fall into two broad categories: B2B (Business-to-Business) and B2C (Business-to-Consumer). Each group has different priorities when investing in CNC technology.
B2B Applications
For businesses that sell, service, or rent machinery, CNC machining centers play a key role in meeting customer demands, reducing downtime, and improving production quality.
Machine Dealers
When I used to work with machine dealers, I noticed that the most successful ones weren’t just selling machines—they were selling confidence. Buyers wanted proof that a CNC machining center could handle their needs before making a purchase.
How do CNC machines help dealers?
- Demonstration Ready: Instead of just talking about a machine’s capabilities, dealers can use a CNC machining center to create sample parts for customers.
- Customization On Demand: Some buyers need slight modifications. Having an in-house CNC machine makes quick adjustments possible.
- Faster Stock Turnaround: Producing small custom parts for clients can add extra value and keep customers coming back.
When customers can see a machine in action, they feel more confident in making a purchase. That’s where CNC machining centers give dealers an edge. If you are in this industry, consider Blue Elephant. Our user-friendly cnc machines come with pre-configured software and training support.
Spare Parts Dealers
Spare parts dealers often stock high-demand components, but what about rare or discontinued parts? CNC machining centers help by:
- Producing Custom Parts: When a manufacturer stops making a part, CNC machines can recreate it with exact specifications.
- Modifying Existing Components: Some parts require adjustments to fit specific models—CNC machining ensures precise alterations.
- Reducing Lead Times: Instead of waiting for suppliers, dealers can produce parts in-house, improving turnaround times.
With CNC machining, dealers can offer better service by providing parts that aren’t easily available elsewhere.
Machine Repairers
Repair specialists rely on precision machining to replace worn-out or damaged parts. CNC machining centers support repair work by:
- Recreating Broken Components: Instead of replacing an entire assembly, CNC machining can fabricate only the damaged part.
- Refinishing Critical Surfaces: CNC milling can restore damaged surfaces to their original tolerances.
- Modifying Parts for Better Performance: Engineers can make minor design improvements to extend part lifespan.
For repair businesses, a CNC machining center reduces reliance on external suppliers and improves service efficiency.
Rental Companies
Rental companies face a different challenge: machine durability. Every rental machine goes through heavy use, and breakdowns mean lost revenue.
CNC machining centers help by:
- Machining Replacement Parts: Instead of replacing entire components, rental companies can machine new ones.
- Improving Maintenance Efficiency: CNC machining makes it easier to create tools and jigs for servicing machines.
- Extending Machine Lifespan: Worn parts can be resurfaced or replaced without waiting on manufacturers.
For rental businesses, CNC machining keeps equipment in service longer, reducing unnecessary expenses.
B2C Applications: Turning Ideas Into Reality
Beyond industrial use, CNC machining centers are changing how products are designed, customized, and manufactured. From furniture makers to signage companies, businesses rely on CNC machines to turn creative ideas into perfectly crafted products.
Furniture Industry
I used to work with a carpenter who built custom furniture by hand. His work was beautiful, but the time it took to make a single piece was limiting his business growth. When he started using a CNC machining center, everything changed.
CNC machining in furniture manufacturing helps by:
- Creating Complex Designs: Intricate carvings and inlays that were once time-consuming are now effortless.
- Reducing Waste: Precision cutting means less material waste, saving money.
- Scaling Production: Once a design is programmed, producing identical pieces is easy.
With CNC machining, businesses can maintain quality while increasing production capacity.
Advertising & Signage
If you’ve ever seen a perfectly engraved company logo, chances are a CNC machine did the work. For sign makers, CNC machining offers:
- Sharp Lettering & Logos: Acrylic, wood, and metal can be cut with perfect detail.
- Custom Shapes & Textures: Raised, layered signage is easy to manufacture.
- Fast Production for Large Orders: High-volume sign production is streamlined.
A CNC machining center allows advertising businesses to offer custom, high-quality signage without manual errors.
Mold Design & Production
Mold makers know how critical accuracy and durability are. CNC machining helps by:
- Cutting High-Precision Molds: Complex cavities are machined with perfect detail.
- Reducing Lead Times: Faster mold production speeds up manufacturing processes.
- Handling Multiple Materials: CNC machining works with metals, plastics, and more.
For industries like automotive, medical devices, and packaging, CNC machining makes the production of complex molds efficient and reliable.
5. Cost Analysis of Investing in CNC Machining Centers
When I was first considering a CNC machining center, the price tag made me pause. Was it really worth it? Could I justify the investment? Like many business owners, I had to weigh the costs vs. long-term benefits.
Investing in a CNC machining center involves several costs beyond just the machine itself. From software and training to maintenance and tooling, understanding these expenses helps in planning your budget effectively. Below is a breakdown of the key cost factors you should consider:
Cost Factor | Description | Estimated Cost |
Initial Purchase Price | Varies based on size, features, and capabilities | $50,000 – $500,000+ |
Software & Programming | Includes CAM software for programming and operation | $1,000 – $15,000 |
Installation & Setup | Professional setup costs for integrating the machine | $5,000 – $20,000 |
Training Costs | Operator training to use and program the machine | $1,500 – $5,000 per operator |
Tooling & Accessories | Cutting tools, tool holders, fixtures, and accessories | $10,000+ |
Maintenance & Repairs | Routine servicing, spare parts, and repair expenses | $3,000 – $10,000 per year |
While the upfront cost is high, CNC machining centers reduce expenses and increase output in ways that manual machining never could.
7. Factors to Consider Before Buying CNC Machining Center
When I was buying my first CNC machining center, I thought bigger was better. I was wrong. The machine I chose had capabilities I didn’t need, and I overlooked key factors like tool changes and production speed. It cost me time and money.
Before making your decision, think beyond just price. Here are four critical tips to help you choose the right CNC machining center for your business.
Tip #1 Choose a Machine That Matches Your Workpiece Material
Not all CNC machines are built for every material. If you pick the wrong one, you’ll face tool wear, poor finishes, or slow machining times.
- Metal: Requires a rigid machine with high cutting power. Best for aerospace, automotive, and heavy manufacturing.
- Plastics: Needs controlled spindle speeds to avoid overheating and melting.
- Wood: Best suited for CNC routers with high-speed spindles for smooth cutting.
- Composites: Requires specialized tooling to avoid fraying or damage.
If you plan to work with multiple materials, check if the machine can adjust speeds, spindle power, and tooling easily.
Tip #2 Match the Machine to Your Production Volume
Are you making custom one-off parts or running a 24/7 production line? Your machine should match your workload.
- Low-Volume Production: Best for prototyping, job shops, and custom work. A smaller CNC machine will work fine.
- Medium-Volume Production: Ideal for batch production where jobs repeat but change frequently. Look for quick setup features.
- High-Volume Production: Requires automation, high-speed spindles, and multi-tool changers to keep up with demand.
If you’re planning to grow your production, get a machine that can scale with your business instead of needing an upgrade too soon.
Tip #3 Check Tool Changer Capabilities for Complex Jobs
If your parts require multiple tools, a slow manual tool change can eat up hours of production time.
- Manual Tool Change: Cheapest, but slows production. Best for small shops with simple parts.
- Basic Automatic Tool Changer (10-20 tools): Good for medium-complexity machining with moderate tool changes.
- Advanced ATC (30+ tools): Necessary for high-precision, multi-tool operations like aerospace or medical machining.
If you’re handling jobs with multiple setups, an automatic tool changer will save time and reduce human error.
Conclusion
I know what it feels like to second-guess a big investment. I’ve been there. But once I saw what a CNC machining center could do, I never looked back.
Now you’ve seen the benefits, the types, the costs, and how they apply across industries. Whether you’re a dealer or product manufacturer, a CNC machining center can bring clarity and capability to your operation.
Blue Elephant builds CNC machining centers designed to meet your real-world challenges with training and support to back it up.
Let’s take your business to the next level—contact us today!
Check Out These Additional Resources
We’ve got more for you! These articles provide more tips and guidance to keep you on track:
Still haven’t found what you’re looking for? Don’t hesitate to contact us. We’re available around the clock to assist you.