I still remember the first time I saw a CNC lathe in action. The machine moved with precision, cutting metal like a hot knife through butter.
I stood there, amazed. How did it know exactly where to move? How could something so powerful be so accurate?
As someone who has worked with CNC machines for years, I understand how confusing they can seem at first. But I’ve also seen how they transform manufacturing, saving time and improving quality.
If you’re wondering what a CNC lathe machine is and why it matters, you’re in the right place. In this article, I’ll break it down in simple terms.
We’ll cover how it works, what it’s used for, and why it’s a game-changer for precision machining. By the end, you’ll understand CNC lathes and how they fit into modern production.
Let’s get started!
1. What is CNC Lathe Machine?
You’ve probably heard the term CNC, but what does it actually stand for? CNC means Computer Numerical Control. It refers to a system where a computer directs the movement of a machine tool using coded instructions.
Instead of manually adjusting dials and levers like in traditional machining, CNC machines follow pre-programmed commands to create precise parts—every single time. This eliminates human error and increases efficiency.
But how does this apply to a lathe?
What Does a CNC Lathe Machine Do?
At its core, a CNC lathe rotates a workpiece while cutting tools shape it. It takes what used to be a hands-on process and automates it for speed and accuracy.
Here’s what the CNC lathe controls:
- Spindle Speed: How fast the workpiece rotates.
- Tool Positioning: The movement of cutting tools for precise shaping.
- Feed Rate: How fast the tool moves against the material.
With this level of automation, you get:
- Faster Production: No constant adjustments, just press start.
- Perfect Consistency: Every part comes out exactly the same.
- Less Waste: More accuracy means fewer mistakes and material loss.
If you need precision, consistency, and faster production, a CNC lathe might be the upgrade you’ve been looking for.
2. How CNC Lathe Machines Work
I still remember watching my first CNC lathe in action. The spindle spun fast, the tool moved with precision, and within seconds, a raw metal piece turned into a perfect part. No manual adjustments, no guesswork—just automated precision at its best.
But how does it actually work?
A CNC lathe machine uses computer programming to control the movement of cutting tools, shaping a workpiece with accuracy and speed. Unlike manual lathes, where the operator guides the tool by hand, CNC lathes follow pre-programmed instructions, making complex machining efficient and repeatable.
Key Elements of a CNC Lathe in Action
- Workpiece Setup: The material is securely clamped in a chuck, ensuring stability as it rotates at high speeds. A poorly secured workpiece can lead to vibration, uneven cuts, or even machine failure.
- Program Input: The machine follows G-code, a set of numerical instructions that dictate every movement. Some shops use CAD/CAM software to convert digital designs into machine-ready code. This eliminates human error and speeds up production.
- Machine Calibration: Cutting tools, spindle speed, and feed rate are set according to the material and job requirements. Harder metals require slower speeds, while softer materials allow for higher cutting rates. Getting these settings right is critical to achieving high-quality finishes and extending tool life.
- Automated Cutting Process: Once programmed and calibrated, the machine begins its automated cutting cycle. Whether it’s turning, drilling, facing, or threading, the lathe executes each cut with extreme precision.
Imagine producing hundreds of identical parts with zero variation. That’s the power of CNC lathes. Whether you’re a machine dealer or repair specialist, understanding how these machines operate gives you an edge—faster production, fewer errors, and lower costs.
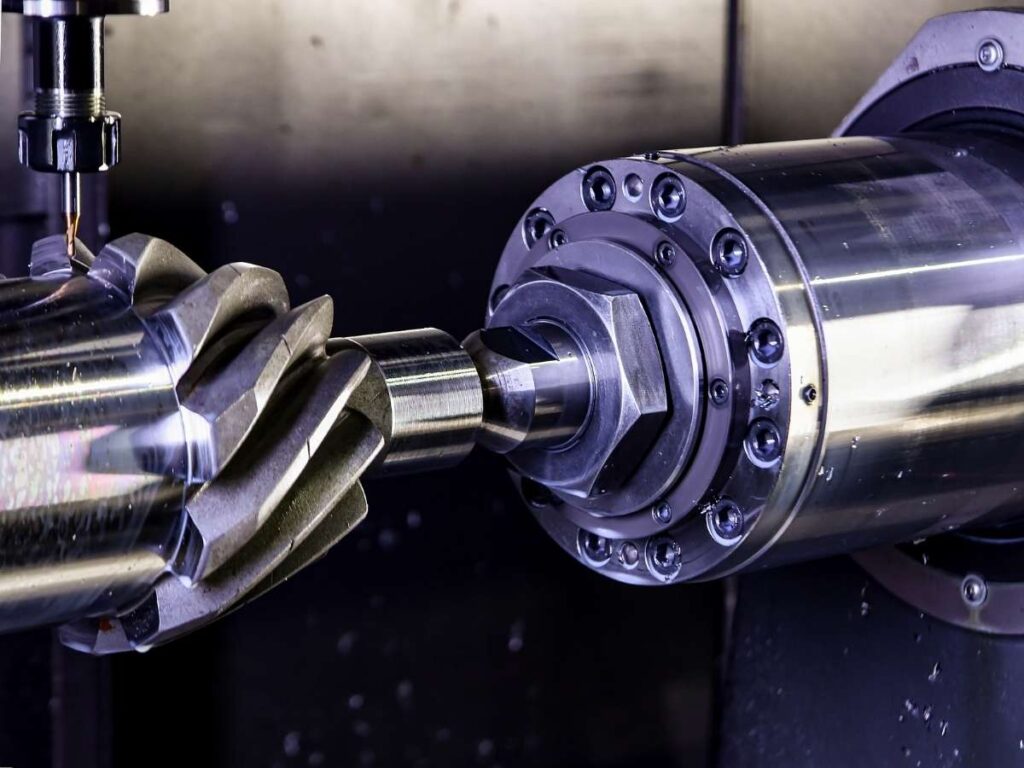
3. Types of CNC Lathe Machines
Not all CNC lathes are the same. The first time I stepped into a shop with multiple types running at once, I was surprised by how specialized they were. Some handled massive parts, while others worked on components so small you needed a magnifying glass to inspect them.
So, how do you know which CNC lathe is right for a job? It depends on the workpiece size, complexity, and precision required. Let’s break down the different types.
Horizontal and Vertical CNC Lathes
A CNC lathe can be classified based on how the spindle is oriented—horizontally or vertically. This affects how the workpiece is held and machined.
A horizontal CNC lathe is the most common type used in manufacturing. The spindle is mounted parallel to the ground, and the workpiece is secured in a rotating chuck. This setup allows for high-speed machining, making it ideal for producing shafts, rods, and other cylindrical components.
A vertical CNC lathe, on the other hand, has the spindle positioned upright. Instead of being held horizontally, the workpiece is clamped in a vertical orientation. This design is perfect for large, heavy, or irregularly shaped parts, such as engine casings and industrial gears. The weight of the workpiece keeps it stable, allowing for deeper cuts without deflection.
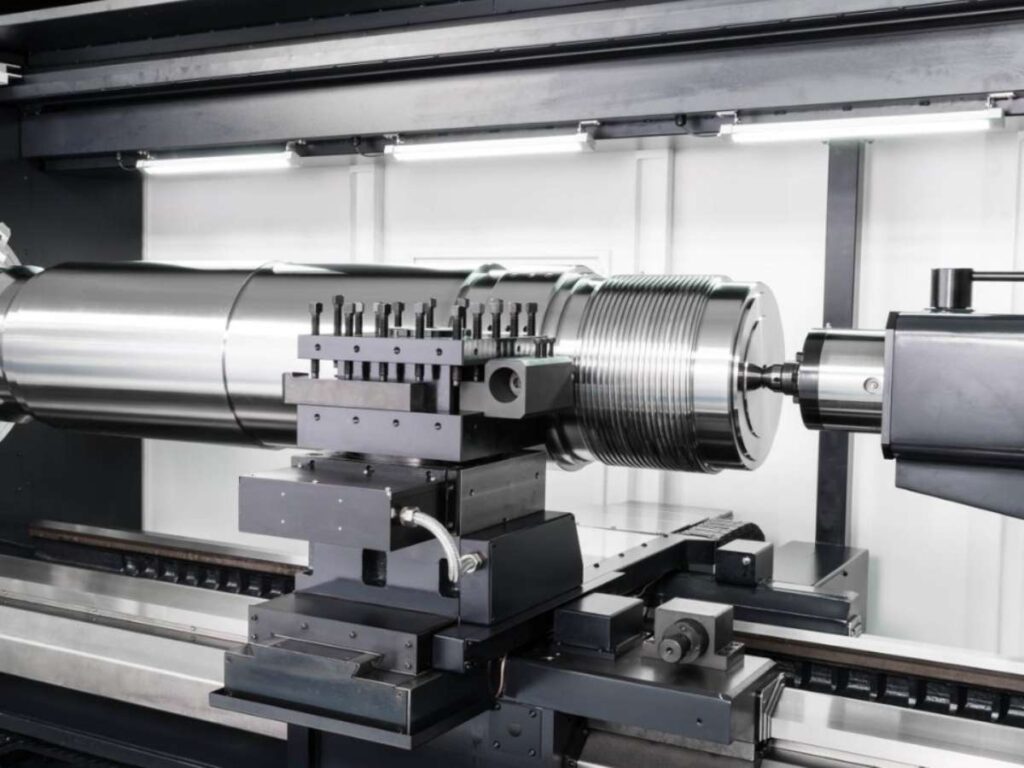
Swiss-Type CNC Lathes: The Master of Small Precision Parts
If you’re in medical, aerospace, or electronics manufacturing, you’ve probably heard of Swiss-type CNC lathes. Unlike traditional lathes, which hold the workpiece at one end, a Swiss lathe supports the material along its entire length, reducing vibration and improving precision.
What makes Swiss lathes unique?
- Perfect for ultra-small, high-precision components like medical implants, watch parts, and aerospace fasteners.
- Minimizes deflection by keeping the workpiece supported at all times.
- Handles complex, multi-operation machining in one setup.
These machines aren’t just precise—they’re essential for industries where a 0.001-inch tolerance can make or break a part.
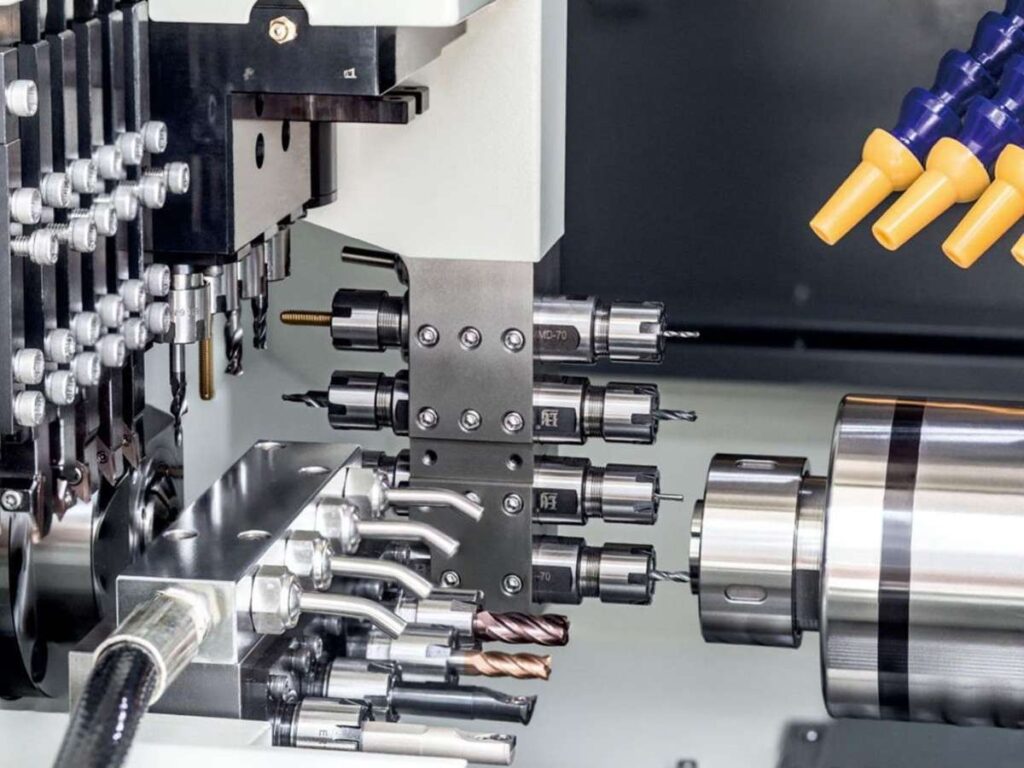
Multi-Axis CNC Lathes: Expanding Capabilities
Traditional lathes move in just two directions—left/right and in/out. But what if you need to add milling, drilling, or cutting angles? That’s where multi-axis CNC lathes come in.
- 2-Axis CNC Lathes: The simplest type, used for basic turning and facing.
- 3-Axis CNC Lathes: Adds a milling spindle for cutting features like slots and holes.
- 4-Axis CNC Lathes: Rotates the workpiece to allow angled cuts and advanced milling.
- 5-Axis CNC Lathes: The most advanced, machining complex 3D shapes in a single setup.
A 5-axis CNC lathe is a game-changer for aerospace and high-precision industries. Imagine machining a turbine blade in one setup instead of repositioning it multiple times. That’s what makes multi-axis machines so powerful.
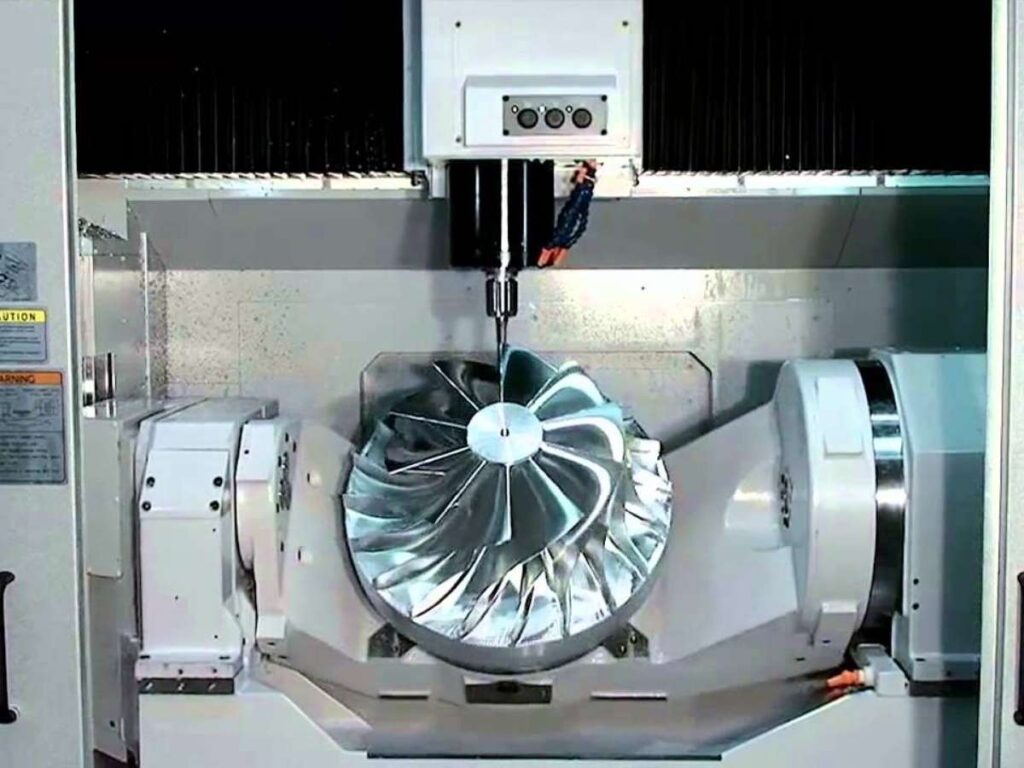
4. Key Features to Look for in CNC Lathe Machine
I’ve seen shops struggle with production simply because they chose the wrong CNC lathe. A machine might have a powerful spindle but lack automation, or it might be fast but unable to handle harder materials. Choosing the right CNC lathe isn’t just about specs—it’s about making sure it fits your production needs and long-term goals.
Spindle Speed and Power
The spindle is one of the most important parts of a CNC lathe. It controls how fast the workpiece rotates and determines how efficiently the machine can cut. A mismatch in spindle speed or power can lead to rough finishes, excessive tool wear, or even machine failure.
- Spindle Speed (RPM): High-speed spindles (6,000+ RPM) are great for aluminum and plastics, while slower speeds with high torque are better for cutting harder metals like titanium and stainless steel.
- Power (Horsepower or Kilowatts): A more powerful spindle handles deeper cuts and harder materials without stalling.
I remember working with a lathe that struggled with stainless steel. Every cut took longer, and the finish was rough. Upgrading to a higher-torque spindle completely changed the process—cuts were faster, smoother, and more precise.
Tool Capacity and Automation Level
The more tools a CNC lathe can hold, the fewer interruptions during machining. A lathe with limited tool slots requires frequent manual tool changes, which adds downtime and reduces efficiency.
- Turret Tool Changers: Typically hold 8–12 tools, making them ideal for basic turning jobs.
- Automatic Tool Changers (ATC): Store 20+ tools, allowing for complex multi-step machining without stopping production.
- Live Tooling Capabilities: Enable drilling, milling, and tapping in a single setup, reducing the need for additional machines.
Automation also plays a big role in efficiency. Lathes with robotic loading systems or bar feeders can run unattended, increasing output while lowering labor costs. The right tool setup means less downtime, faster production, and higher profit margins.
Material Compatibility
Not all CNC lathes are designed to cut every material. Some are optimized for metal machining, while others handle plastics, composites, or even wood. Using the wrong machine for your material can result in poor accuracy, tool damage, or excessive maintenance costs.
- Metals: Steel, aluminum, brass, and titanium require high spindle torque, strong tool holders, and cooling systems to prevent overheating.
- Plastics & Composites: These materials need lower cutting speeds and sharp tool edges to avoid melting or fraying.
- Wood: CNC lathes for wood often have high-speed spindles and efficient dust collection for cleaner cuts.
If you’re primarily working with one material, getting a specialized lathe makes sense. But if your work varies, a versatile machine with adjustable settings is a smarter investment.
5. CNC Lathe Machine Applications
CNC lathes have changed the way industries approach manufacturing. Whether it’s a factory producing thousands of precision parts or a small business creating custom designs, these machines streamline production, improve accuracy, and reduce manual labor. Some industries rely on them for mass production, while others use them for one-of-a-kind custom work.
Let’s take a look at how CNC lathes fit into both large-scale industrial applications and smaller, end-user projects.
Industrial Applications (B2B)
For manufacturers and machine shops, CNC lathes provide high precision, repeatability, and efficiency in large-scale production. These industries depend on them for creating durable, consistent parts.
- Metalworking Industries: Automotive, aerospace, and oil & gas sectors use CNC lathes for engine components, hydraulic fittings, and structural parts that require tight tolerances and reliable performance.
- Mold and Die Manufacturing: CNC lathes create precise molds and dies used in plastic injection molding and metal casting. A small imperfection in a mold can ruin an entire batch, making CNC accuracy essential.
- High-Volume Mechanical Component Production: Bearings, gears, fasteners, and shafts must be identical across thousands of units, and CNC automation allows for fast, uniform production.
- Spare Parts Manufacturing and Repair Services: Many industries can’t afford long downtimes, so CNC lathes are used to reproduce worn-out parts quickly and on-site, reducing delays and costs.
I once visited a machine shop that specialized in making aerospace parts. Every component had to meet exact specifications—even the smallest deviation could cause performance issues. Their CNC lathe allowed them to machine parts with unmatched consistency, ensuring reliability in high-stress environments.
End-User Applications (B2C)
While large industries rely on CNC lathes for mass production, smaller businesses and creative professionals use them for custom work, prototyping, and design projects.
- Furniture and Woodworking: CNC lathes carve intricate table legs, chair spindles, and decorative wood elements with perfect symmetry, making custom furniture production faster and more precise. If you are in this industry and looking for a reliable CNC lathe machine supplier, consider Blue Elephant.
- Advertising and Signage Production: CNC-machined metal and plastic signs provide crisp, professional branding for businesses. Precision cutting allows for intricate lettering and design work.
- Custom Decoration and Crafts: Jewelers, engravers, and artists use CNC lathes to create personalized metal, wood, and plastic items that would be nearly impossible to replicate by hand.
- Prototyping and Small-Batch Manufacturing: Engineers and product designers use CNC lathes to create working prototypes before committing to large-scale production. This saves money and allows for easy design modifications.
A small business owner once told me how his CNC lathe transformed his woodworking shop. What used to take hours of manual carving was now done in minutes, allowing him to take on more custom orders without sacrificing quality.
6. Required Maintenance of CNC Lathe Machine
A CNC lathe is a powerful tool, but like any machine, it only performs well if it’s properly maintained. I’ve seen shops try to push their lathes to the limit without regular upkeep, only to deal with costly breakdowns and production delays. Keeping your CNC lathe in top shape doesn’t have to be complicated, but it does require consistency.
Here’s some of the required maintenanance.
Regular Lubrication of Moving Parts
Friction is the enemy of any machine. A CNC lathe has spindles, guide rails, and ball screws that move constantly, and without proper lubrication, these parts can wear down quickly.
- Use manufacturer-recommended lubricants to reduce wear and prevent overheating.
- Check oil levels and grease fittings regularly to keep motion smooth.
- Clean and replace old or contaminated lubricant—dirty oil can cause more harm than good.
Skipping lubrication might not cause immediate failure, but over time, you’ll start to notice rough movements, increased vibration, and decreased accuracy.
Inspection and Replacement of Cutting Tools
A dull or damaged tool doesn’t just affect part quality—it puts extra strain on the machine and increases cycle times.
- Inspect tools daily for chipping, dull edges, or excessive wear.
- Replace cutting inserts before they become too worn, avoiding poor surface finishes.
- Check tool alignment and positioning to prevent unnecessary tool breakage.
CNC Control System Updates and Backups
A CNC lathe relies on software and electronic components just as much as mechanical parts. Keeping the control system updated and backed up is crucial for long-term performance.
- Regularly update firmware and control software to improve efficiency and fix known bugs.
- Backup machine parameters and tool offsets to avoid losing settings in case of a failure.
- Inspect wiring and connections for signs of wear, especially in high-vibration environments.
I once saw a machine lose its calibration completely after a sudden power outage. The operator had no backup of the settings, and it took hours to reprogram everything. Having a backup file on hand can prevent these headaches and get your machine running again quickly.
7. Tips on How To Choose The Best CNC Lathe Machine
Buying a CNC lathe is a major investment, and I’ve seen companies make costly mistakes by choosing a machine that doesn’t fully meet their needs. Some end up with too little power, struggling with tough materials, while others overspend on features they never use. The right CNC lathe isn’t just about having the latest specs—it’s about matching the machine to your production needs and long-term goals.
Here are the top factors to consider before making an investment.
Tip #1 Choose the Right Machine Specifications
A CNC lathe needs to match your production demands. The wrong spindle speed, tool capacity, or control system can slow you down and increase costs. Before purchasing, ask yourself: What types of parts will you produce? What materials will you work with? How much automation do you need?
- Spindle Speed: If you’re working with soft materials like aluminum, go for higher RPMs (6,000+ RPM). For harder metals like stainless steel or titanium, lower speeds with higher torque are essential.
- Tool Capacity: If you’re machining complex parts, look for a lathe with automatic tool changers and live tooling to reduce setup time and improve efficiency.
- Control System: Some CNC lathes have advanced programming interfaces, while others focus on user-friendly operation. Make sure the system fits your team’s skill level.
Tip #2 Evaluate the Manufacturer’s Reputation
Not all CNC lathe manufacturers are created equal. Some manufacturers prioritize durability and customer support, while others cut costs by using lower-quality components. Before committing, take the time to research who you’re buying from.
- Industry Reviews: What do other machine shops say about the brand? Are their lathes reliable, or do they break down often?
- Support and Warranty: A good manufacturer provides strong technical support, training, and readily available replacement parts.
- Parts Availability: If a machine part fails, how quickly can you get a replacement? Long wait times mean costly downtime.
At Blue Elephant, we offer 24/7 online support, spare parts supply, and on-site servicing when needed. We also share case studies, testimonials, and certifications, and offer trial orders.
Tip #3 Balance Investment and ROI (Return on Investment)
Many buyers focus too much on the initial price and ignore the long-term impact. A CNC lathe should be evaluated based on total cost of ownership, including maintenance, tool life, and efficiency.
- Energy Efficiency: Some machines consume less power, lowering operating costs over time.
- Production Speed: Faster cycle times mean higher output and better profitability.
- Automation Features: Investing in automatic tool changers and robotic loading systems may cost more upfront but reduce labor costs significantly.
A shop I worked with hesitated to buy a higher-end CNC lathe due to the cost. But once they calculated faster cycle times, reduced tool wear, and lower scrap rates, they realized it would pay for itself within a year. Thinking beyond the purchase price led to a smarter investment.
Conclusion
CNC lathe machines are smarter, faster, and more efficient than ever. From AI-driven automation to hybrid manufacturing, the industry is evolving at a rapid pace.
I’ve seen shops struggle with outdated processes. I’ve also seen businesses embrace change and thrive. The difference? Taking action.
At Blue Elephant, we specialize in high-precision CNC machines built for the future. We also provide remote guidance or send engineers for on-site assistance.
Contact us today and let’s build something incredible.
Learn More: Recommended Reads
Want to see more products? We’ve got plenty of options that might just be the perfect fit for you:
Still haven’t found what you’re looking for? Don’t hesitate to contact us. We’re available around the clock to assist you.