The first time I had to order CNC machine tools, I was stuck. I knew what I needed, but I didn’t know what they were called. The result? A delayed order and wasted time.
If you’ve been in that situation, you know how frustrating it is. A simple reference list could have saved me the headache—and that’s exactly what this guide is for.
Having worked with manufacturers and suppliers, I know the importance of precision—not just in machining but in communication. This list is built from real-world experience, providing accuracy and relevance.
Inside, you’ll find an easy-to-follow breakdown of CNC machine tools, their uses, and how they apply to different machining processes. Whether you’re ordering parts or training your team, this guide has you covered.
So, let’s jump in!
1. CNC Milling Machine Tools
CNC milling machines are some of the most versatile tools you’ll come across in a machining environment. Whether you’re roughing out a simple rectangular block or finishing a complex aerospace component, milling gets the job done with precision. And if you’re running a shop, these machines probably do a good chunk of the daily workload.
- End Mills: These are your go-to cutters, and probably the first tool you’ll get familiar with. lat end mills are great for sharp corners and edges, while ball nose end mills give you those clean curves when working on 3D parts.
- Face Mills: When you need to flatten a surface quickly and with a nice finish, face mills are the way to go. I’ve used them mostly for prepping stock before fine machining, and they do a clean job thanks to their multiple cutting edges. They’re fast, efficient, and make a noticeable difference in surface quality.
- Slot Drills: These come in handy when you need to plunge straight down into a workpiece. I’ve used them for slotting and pocketing jobs where accuracy matters and a regular end mill just won’t cut it, literally.
- Fly Cutters: These tools move a bit slower, but the results are worth the wait. Fly cutters use a single-point cutting tool to produce a very smooth, polished finish, perfect when surface quality is non-negotiable, like in aerospace or die-making projects.
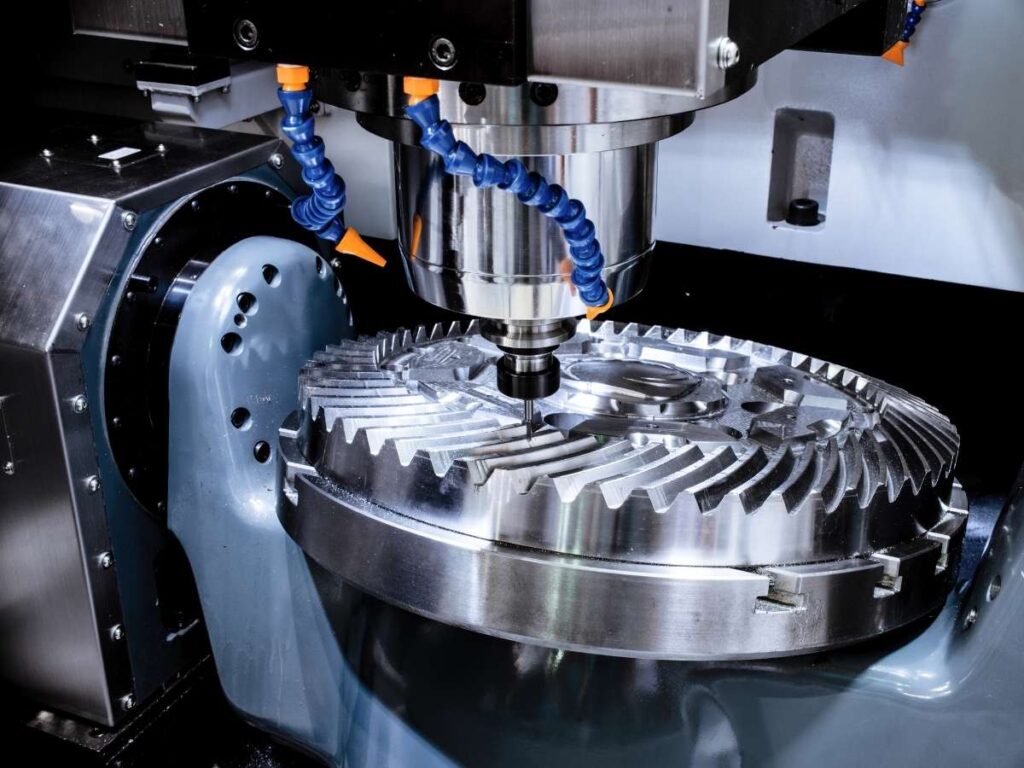
2. CNC Turning Machine Tools (Lathe Tools)
The first time I operated a CNC lathe, I remember being surprised by how calm the process looked on the outside and how much precision it actually demanded behind the scenes. There’s something almost therapeutic about watching a piece of spinning metal slowly take shape into a perfectly machined part.
- Turning Inserts: These are the replaceable tips that do the actual cutting. I’ve worked mostly with carbide inserts, which are great for long runs and tougher materials. They come in shapes like triangles, rounds, and diamonds, each meant for specific cutting tasks such as roughing or finishing.
- Boring Bars: These are used when you need to enlarge a hole or fine-tune its inner diameter. Since they’re often working deep inside a part, they need to be extremely rigid to avoid vibration and maintain dimensional accuracy.
- Parting (Cut-off) Tools: This tool comes into play when you’re ready to finish the part and separate it from the rest of the stock. It has a thin cutting edge that gives you a clean break with very little material waste.
- Threading Tools: These tools carve precise threads into the workpiece by following a controlled path. Whether you’re cutting internal or external threads, these tools are built for consistency, which is critical in industries where fit and function have zero room for error.
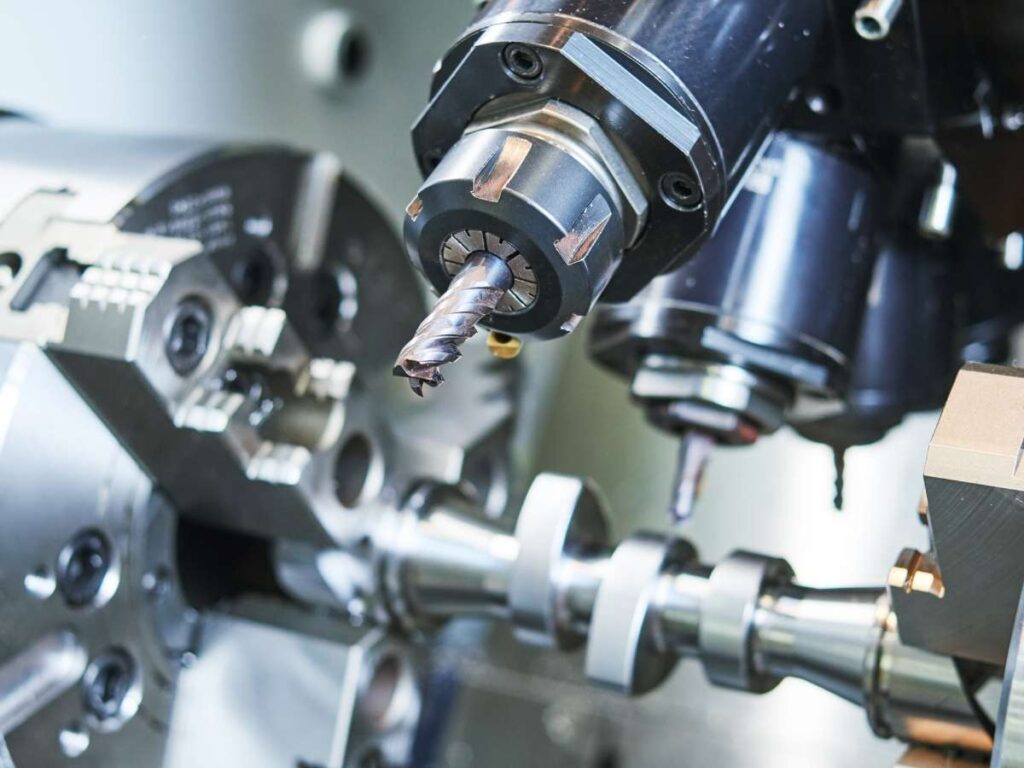
3. CNC Drilling Machine Tools
CNC drilling machines take that process and make it incredibly consistent. With the right tools in the spindle, you can knock out hundreds of holes with the same precision every time. Here are the core tools I’ve relied on to get the job done right:
- Twist Drills: These are the go-to in most shops, and for good reason. The spiral flutes do a great job pulling chips up and out of the hole while the bit keeps cutting cleanly. I prefer drills with coatings like titanium nitride because they last longer and hold up better when you’re dealing with tougher metals.
- Center Drills: If I’m drilling into round bar or anything slick, I always start with a center drill. They help create a precise starting point so the twist drill doesn’t wander, which is especially important in parts that require tight alignment.
- Countersinks: These come into play whenever I need to seat a flat-head screw flush with the surface. I usually keep a few different angles on hand, but 82 degrees covers most of the jobs I run into.
- Counterbores: When a bolt head needs to sit below the surface, this tool does the trick. I’ve used it a lot in assembly-heavy projects where clean finishes matter and the heads can’t stick out.
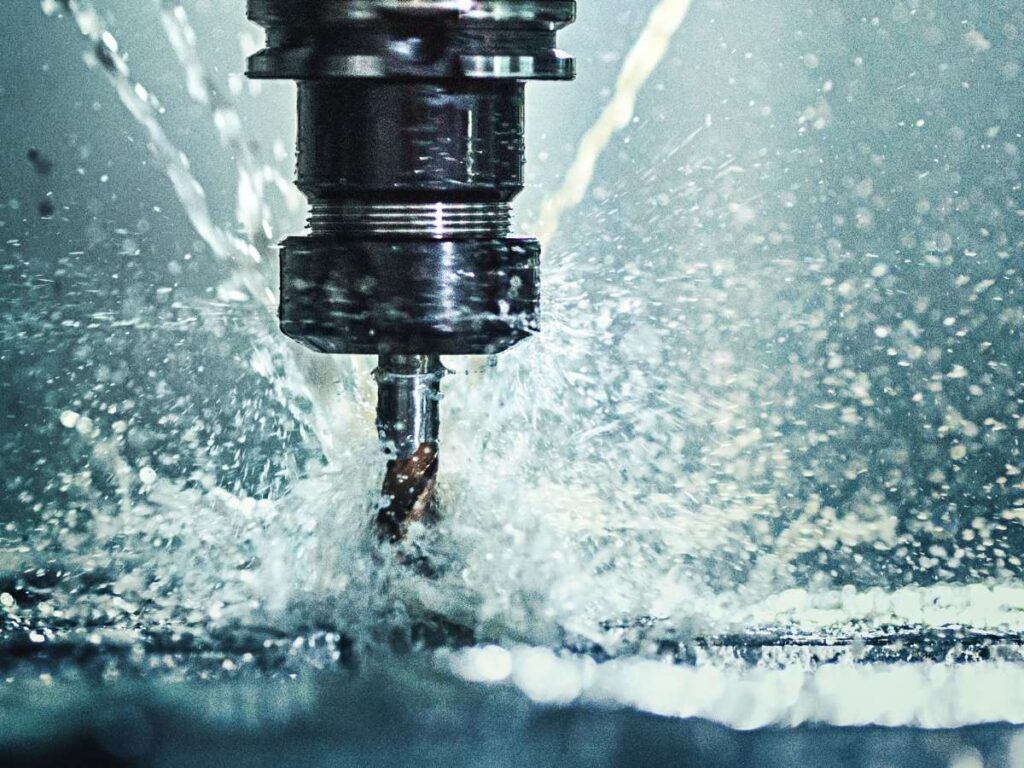
4. CNC Grinding Machine Tools
Grinding was one of those processes I didn’t fully appreciate until I saw it fix what milling couldn’t. There’s something satisfying about getting that final surface finish just right, especially when you’re dealing with tight tolerances. It’s not the flashiest part of machining, but when you need precision, grinding steps in where other tools fall short.
- Surface Grinding Wheels: These are what I use when I need a perfectly flat surface. It’s often the last step in the process, where every micrometer matters. I’ve relied on surface grinding to clean up parts that need to meet strict tolerances, and it always delivers the finish I’m after.
- Cylindrical Grinding Wheels: These come into play when working on round parts like shafts, pins, or bearing journals. I’ve used them to get surfaces so smooth they feel polished to the touch, which is key in rotating components where any surface imperfection could lead to wear or imbalance.
- Centerless Grinding Wheels: When I need to grind a bunch of small round parts quickly and consistently, centerless grinding is the way to go. Since it doesn’t require centers to hold the workpiece, it saves time and makes mass production of precision parts like fuel injectors a whole lot easier.
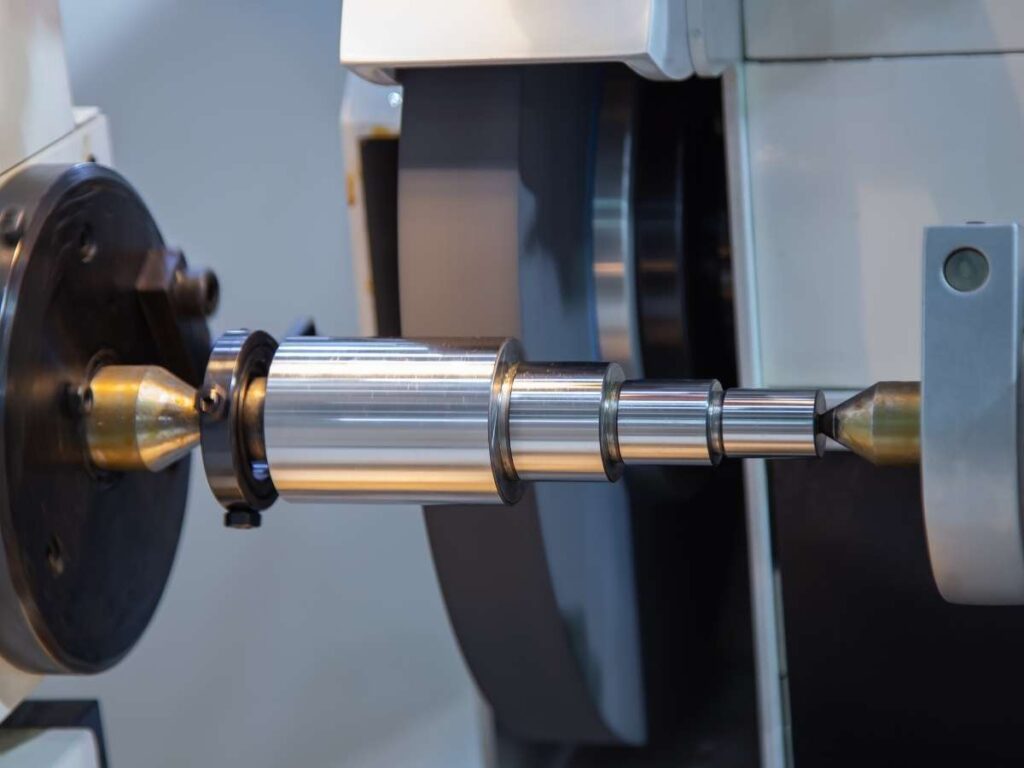
5. CNC EDM (Electrical Discharge Machining) Tools
EDM uses electrical discharges to erode material instead of physically cutting it. It’s especially helpful when you’re dealing with hard metals or intricate geometries that milling or turning just can’t handle efficiently. Here are the tools that make it all happen:
- Sinker EDM Electrodes: These are shaped electrodes made from copper, graphite, or tungsten. I’ve used them for mold cavities and detailed forms, and they’re incredibly precise. The electrode and workpiece are both submerged in dielectric fluid, and the spark erosion removes material layer by layer without any direct contact.
- Wire EDM Wires: This setup uses a thin wire, often brass or molybdenum, to slice through metal with impressive precision. It’s a favorite in industries like aerospace and medical, where ultra-tight tolerances and clean finishes are standard expectations.
- Dielectric Fluid Systems: The dielectric fluid plays a huge role in the EDM process. It cools the work area, prevents stray arcing, and flushes away debris so the spark stays clean. I always make sure this system is well-maintained because a dirty tank or clogged filter can affect everything from surface finish to tool life.
- Electrode Wear Monitoring Systems: Since EDM tools break down slowly during use, monitoring wear is critical for long or detailed jobs. Machines with automatic wear tracking help keep accuracy in check, even as the electrode erodes. It’s one of those behind-the-scenes features that keeps parts within spec.
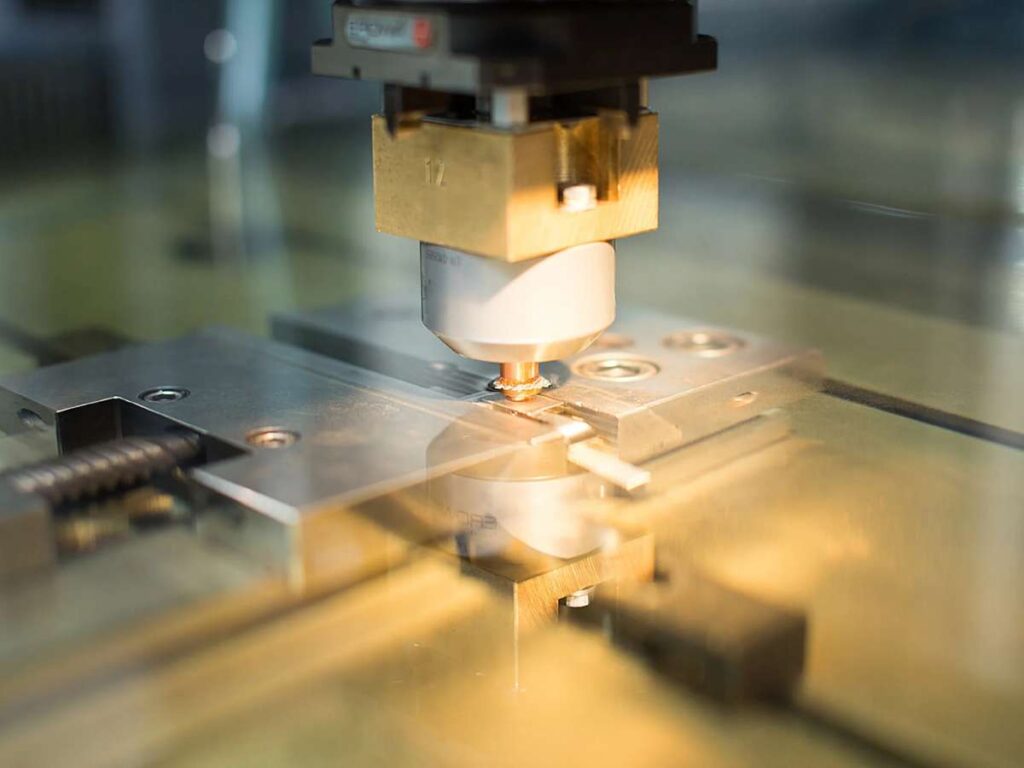
6. CNC Plasma and Laser Cutting Tools
Both plasma and laser cutters bring speed and precision to the table. If you’re in metal fabrication, automotive, or aerospace, there’s a good chance you’ve already leaned on one of these systems to keep production moving efficiently.
- Plasma Cutting Torches: These torches use ionized gas to melt through conductive metals like steel, aluminum, and copper. What I like about plasma cutting is how quickly it handles thicker materials, making it a solid choice for heavy-duty work like brackets or structural components.
- High-Frequency Plasma Generators: Plasma cutters depend on high-voltage power to create and control the plasma arc. With modern digital generators, I’ve been able to fine-tune power settings to get much cleaner edges and reduce post-processing time.
- CNC Laser Cutting Heads: Laser cutters use concentrated beams from CO2, fiber, or Nd:YAG sources to deliver incredibly fine and accurate cuts. They’re my go-to for detailed tasks like logo engraving or cutting thin sheet metal where aesthetics matter just as much as function.
- Assist Gas Systems: Using gases like oxygen, nitrogen, or compressed air, these systems improve cut quality and speed. I’ve seen noticeable gains when using oxygen for steel—it speeds things up and gives you cleaner cut edges thanks to the oxidation boost.
- Beam Focusing Lenses: The laser beam only performs as well as the lens allows. I always make a point to keep lenses clean and aligned, because even a small smudge can mess with accuracy, especially on tight-tolerance jobs.
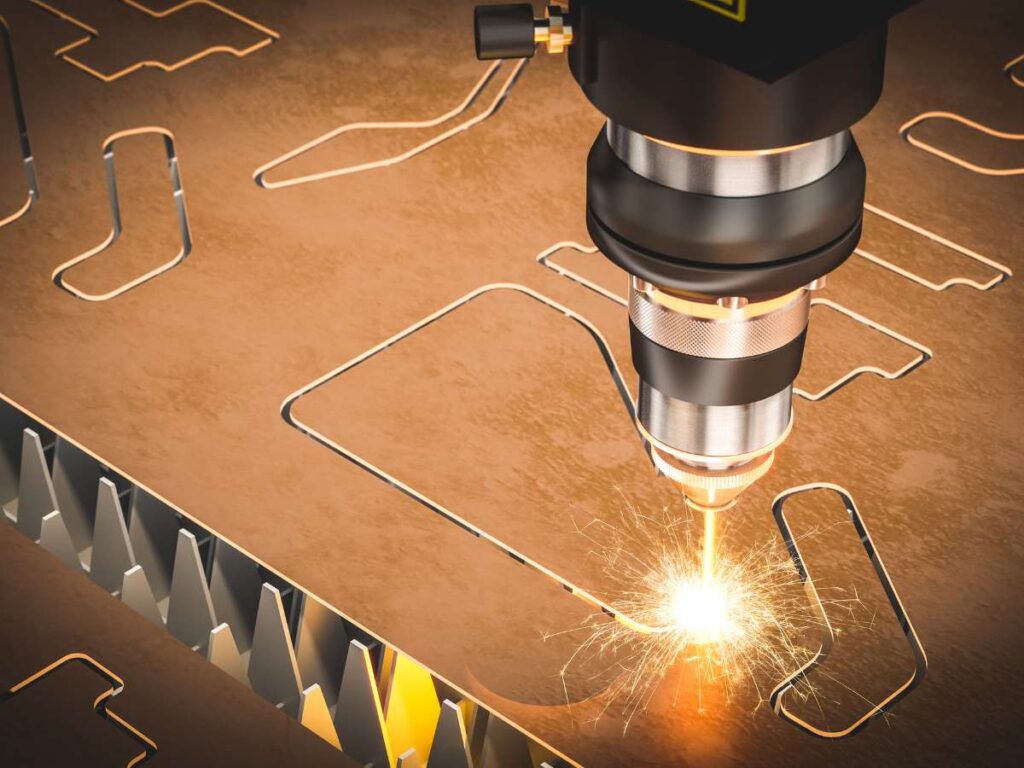
7. CNC Waterjet Cutting Tools
CNC waterjet cutting is one of the most versatile methods out there. It can handle everything from soft rubber to thick steel, all without altering the material’s properties. It’s a favorite in industries like metal fabrication, aerospace, and stone work for good reason.
- Abrasive Waterjet Nozzles: When I need to cut through hard or thick materials like steel or stone, this is my first choice. By adding garnet or aluminum oxide to the water stream, the cutting power increases significantly, making it possible to get precise cuts through materials that would wear out other tools.
- Pure Waterjet Nozzles: These are great for softer materials where abrasives would be overkill. I’ve used them on foam and rubber parts where a clean edge is just as important as avoiding deformation, and they do the job without leaving burn marks or warping.
- High-Pressure Pumps: These pumps are the muscle behind the operation, generating between 30,000 and 90,000 psi. The difference in cut quality and speed between mid-range and high-end pumps is noticeable, especially when you’re working with dense materials.
- CNC Motion Control Systems: Precision is everything with a waterjet. I’ve worked on machines with advanced motion controllers that follow complex paths with ease, allowing for detailed cuts in marble and even glass. Once you’ve dialed in the motion system, the creative possibilities really open up.
- Water Recycling Systems: I’ve always appreciated when a shop runs efficiently, and water recycling is a big part of that. These systems help cut down on waste and keep costs in check, especially if you’re running jobs daily. Plus, it’s a great way to reduce environmental impact without sacrificing performance.
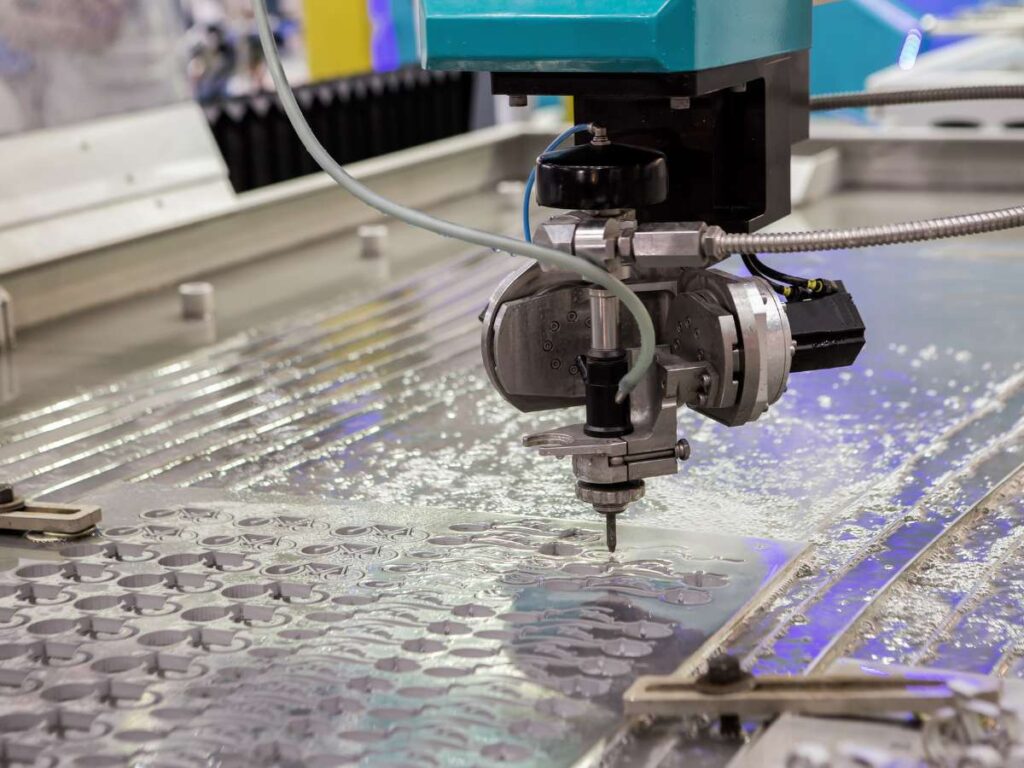
8. CNC Router Tools
CNC routers are high-speed cutting machines built for wood, plastic, aluminum, and composite materials. You’ll find them in shops that do cabinetry, custom displays, and everything in between.
- Straight Bits: These are some of the most-used bits in router setups. I’ve relied on them for cutting grooves, dados, and straight edges—they leave clean results and don’t cause much tear-out when the feed rate is dialed in correctly.
- V-Bits: Great for engraving text or decorative patterns, V-bits give your work a polished, professional finish. The sharp angle of the bit lets you create details that really stand out, especially in sign-making projects.
- Ball Nose Bits: These are my go-to when I need smooth 3D curves or contoured surfaces. They’re essential for projects that involve carving artistic features or working with rounded edges in wood or foam.
- Flush Trim Bits: When I’m following a template or pattern, this bit saves a ton of time. The bearing on the tip rides along the edge while the cutter trims everything perfectly to match—it’s especially useful for laminate work and furniture panels.
- Compression Bits: These are the answer to clean edges on both sides of a sheet. With both upcut and downcut flutes, they prevent chipping on plywood, MDF, and laminated materials, which means less sanding and a more finished look right off the machine.
9. CNC Tool Holders and Accessories
Tool holders and accessories make sure your cutting tools stay stable, accurate, and safe during operation. The right setup can improve tool life, reduce wear on your machine, and give you cleaner, more reliable results.
- Collet Chucks: These are one of the most common ways to hold tools securely. I’ve used ER collets in many general machining setups because they handle a range of tool sizes and help keep runout to a minimum.
- End Mill Holders: These use a set screw to lock the tool in place. I like using them for roughing or heavy-duty milling where I need a stronger grip and don’t want any movement in the tool.
- Hydraulic Tool Holders: These use internal hydraulic pressure to apply even clamping force around the tool. I’ve used them for high-speed finishing work, and they really help reduce vibration and improve accuracy.
- Shrink Fit Tool Holders: This type uses heat to expand the holder before inserting the tool. As it cools, it tightens around the tool with incredible grip. It takes a bit more time to set up, but the stability is worth it for tight-tolerance jobs.
- Tool Presetters: These are a time-saver on the shop floor. By measuring and setting tool lengths and diameters offline, I can speed up machine setups and avoid delays during production.
- Coolant Delivery Systems: Keeping the tool cool is just as important as keeping it sharp. I’ve worked with flood systems, misting units, and through-spindle coolant setups. Each one plays a role in reducing heat and improving cut quality.
- Chip Conveyors: Chips build up fast during production runs. A good conveyor keeps the workspace clear, reduces tool interference, and helps the machine keep running without interruption.
Conclusion
I started this guide thinking back to when I didn’t know a collet from a compression bit.
You’ve now got a quick reference for every essential CNC machine tool, and that’s powerful.
Use it at the shop. Share it with your team. Come back to it anytime you hit a roadblock.
So what’s your next move? Which part of your process could run smoother with the right tool?
Let’s figure it out together.
Contact Blue Elephant today to get the machines and support you need to level up.
Explore More Helpful Resources
Need more ideas? Browse through our extended range of products and discover something new:
Want to learn more? Here are some articles filled with valuable tips and information to guide you further:
- CNC Machine Definition
- CNC Insert Name List: A Quick Reference Guide
- Top 9 Fiber Laser Cutting Machine Manufacturers
Still haven’t found what you’re looking for? Don’t hesitate to contact us. We’re available around the clock to assist you.